Method for detecting longitudinal force of steel rail based on transverse vibration characteristic of steel rail
A technology of lateral vibration and longitudinal force, which is applied in the field of transportation, can solve the problems of not reflecting the stress distribution, the influence of the state of the rail itself, and the accuracy of the detection results have not been verified, so as to achieve high reliability, less time-consuming, and avoid manual operation Effect
- Summary
- Abstract
- Description
- Claims
- Application Information
AI Technical Summary
Problems solved by technology
Method used
Image
Examples
Embodiment 1
[0027] Embodiment 1: as figure 1 , 2 , 3, the present embodiment specifically relates to a method for detecting the longitudinal force of the rail based on the lateral vibration characteristics of the rail, which specifically includes the following steps:
[0028] (1) if figure 1 , 2 As shown, the sleepers 1 are evenly spaced, the distance between the sleepers is d, and a layer of under-rail backing plate 2 is arranged on the upper surface of each sleeper 1, and the rails 4 on both sides are arranged above each sleeper 1 longitudinally, and pass through the rail Fasteners 3 are buckled and fixed to form a seamless line;
[0029] Install several acceleration sensors 5 along the longitudinal interval at the bottom of one side of the seamless line rail 4, the number of acceleration sensors 5 should be at least 3 or more, and each acceleration sensor 5 should be arranged in the middle position between adjacent sleepers 1 , that is, at the 1 / 2 spacing position between adjacent ...
Embodiment 2
[0041] Embodiment 2: as figure 1 , 2 , 3, the present embodiment will be described by substituting actual engineering data on the basis of the method in embodiment 1, specifically as follows:
[0042] (1) Several acceleration sensors 5 are installed at the bottom of the rail 4 on one side of the seamless line along the longitudinal interval. Each acceleration sensor 5 should be set in the middle position between adjacent sleepers 1, that is, 1 / 2 spacing position;
[0043] (2) if figure 1 , 2 As shown, the mass of rail 4 per unit length is 60kg / m, and the sleeper spacing d is measured to be 0.60m. According to the following table, the corresponding "rail lateral vibration resonance frequency - rail temperature change" fitting can be determined. Curve f=A*t+B=-0.1910t+570.3837, where: t represents the temperature change of the rail, the unit is ℃;
[0044]
[0045] (3) Hit the rail waist of the rail 4 laterally with a force hammer at the position where the acceleration ...
PUM
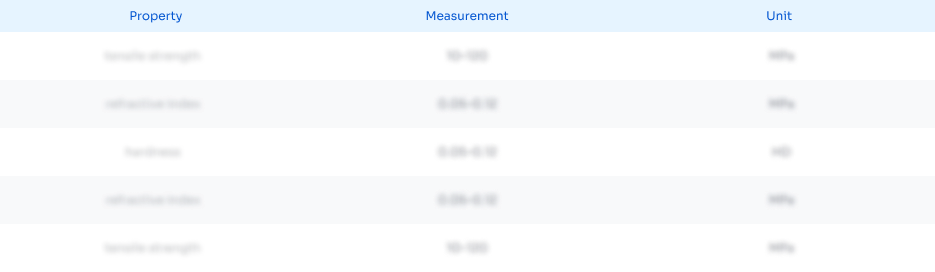
Abstract
Description
Claims
Application Information

- R&D
- Intellectual Property
- Life Sciences
- Materials
- Tech Scout
- Unparalleled Data Quality
- Higher Quality Content
- 60% Fewer Hallucinations
Browse by: Latest US Patents, China's latest patents, Technical Efficacy Thesaurus, Application Domain, Technology Topic, Popular Technical Reports.
© 2025 PatSnap. All rights reserved.Legal|Privacy policy|Modern Slavery Act Transparency Statement|Sitemap|About US| Contact US: help@patsnap.com