Padder replacement setting machine loading pre-setting technology
A setting machine and pre-styling technology, applied in the fiber type, textile material processing, liquid/gas/vapor textile processing and other directions, can solve the problems of increasing the difficulty of raising fluff, high repair rate, long production time, etc. Long processing time, good brushing effect and good stability
- Summary
- Abstract
- Description
- Claims
- Application Information
AI Technical Summary
Problems solved by technology
Method used
Examples
Embodiment 1
[0022] A rolling car instead of a sizing machine feeding and presetting process, the process includes the following steps in sequence:
[0023] (1) Dehydration of the dyed cloth: the dyed cloth is dehydrated by a centrifugal dehydrator, the dehydration process: the rotating speed is 2000 rpm, and the running time is 10 minutes; the dyed cloth is a pure polyester warp knitted fabric.
[0024] (2) Feeding by rolling car at room temperature: using a rolling car for padding and loading,
[0025] The rolling solution is: penetrating agent WTB-102 3%, fluffing agent QM758 5%, water 92%; the temperature of the rolling solution is controlled at 40-50°C;
[0026] Rolling process: roll air pressure 0.25 MPa, speed 30m / min;
[0027] (3) Dehydration and wet napping: use a centrifugal dehydrator for dehydration. The dehydration process: the speed is 2000 rpm, and the running time is 6 minutes. The damp cloth obtained after dehydration is firstly sorted, and the fabric is sorted by a tensi...
Embodiment 2
[0032] A rolling car instead of a sizing machine feeding and presetting process, the process includes the following steps in sequence:
[0033] (1) Dehydration of the dyed cloth: the dyed cloth is dehydrated by a centrifugal dehydrator, the dehydration process: the rotating speed is 2000 rpm, and the running time is 10 minutes; the dyed cloth is a pure polyester warp knitted fabric.
[0034] (2) Feeding by rolling car at room temperature: using a rolling car for padding and loading,
[0035] The rolling liquid is composed of the following raw materials in mass fraction:
[0036] Sulfated castor oil 0.008%,
[0037] Sodium alkyl sulfosuccinate 0.012%,
[0038] Hydroxy silicone oil emulsion 0.02%,
[0039] Coconut Oil Fatty Acid Diethanolamide 0.01%,
[0040] Glacial acetic acid 0.001%,
[0041] The balance is water.
[0042] The temperature of the rolling liquid is controlled at 40-50°C; the rolling process: the pressure of the roll is 0.25 MPa, and the speed is 30m / min; ...
PUM
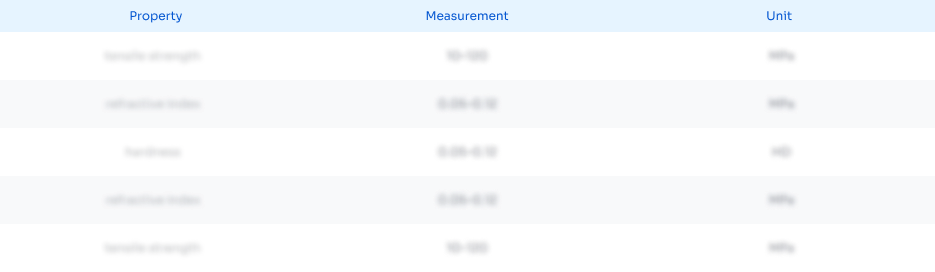
Abstract
Description
Claims
Application Information

- Generate Ideas
- Intellectual Property
- Life Sciences
- Materials
- Tech Scout
- Unparalleled Data Quality
- Higher Quality Content
- 60% Fewer Hallucinations
Browse by: Latest US Patents, China's latest patents, Technical Efficacy Thesaurus, Application Domain, Technology Topic, Popular Technical Reports.
© 2025 PatSnap. All rights reserved.Legal|Privacy policy|Modern Slavery Act Transparency Statement|Sitemap|About US| Contact US: help@patsnap.com