Aluminum alloy underframe of full-loading bus
An aluminum alloy, full load-bearing technology, applied in load-bearing body structures, vehicle parts, superstructures, etc., can solve problems such as increased cost and weight, stress concentration at welding points, and decreased mechanical properties, so as to enhance product competitiveness and extend product life. The life of the chassis, the effect of canceling the electrophoresis process
- Summary
- Abstract
- Description
- Claims
- Application Information
AI Technical Summary
Problems solved by technology
Method used
Image
Examples
Embodiment Construction
[0033] The present invention will be described in detail below in conjunction with the accompanying drawings.
[0034] An aluminum alloy underframe for a full load passenger car, comprising a front underframe 1, a middle underframe 2, a rear underframe 3, a front middle floor frame 4 and a rear floor frame 5; the front underframe 1 is arranged on the bottom The front end of the frame, the rear end of the front chassis 1 is welded to the front end of the middle chassis 2; the rear chassis 3 is arranged at the rear end of the chassis, and the front end of the rear chassis 3 is welded to the rear end of the middle chassis 2; The front and middle floor frame 4 is arranged at the front and middle of the chassis, and is welded with the front chassis 1 and the middle chassis 2 respectively; 3 Welding; the left and right sides of the underframe are riveted and welded with the left and right side frame of the aluminum body respectively; the front end of the underframe is welded with th...
PUM
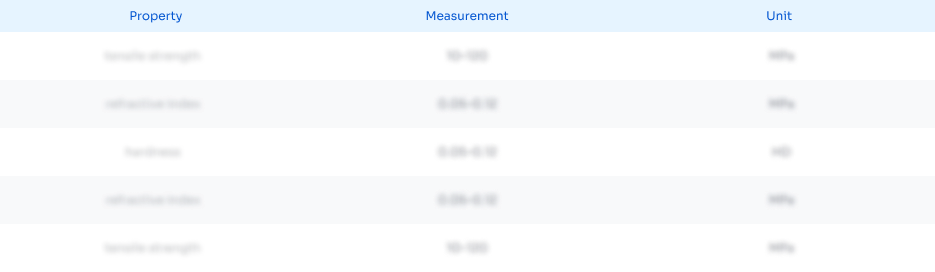
Abstract
Description
Claims
Application Information

- R&D Engineer
- R&D Manager
- IP Professional
- Industry Leading Data Capabilities
- Powerful AI technology
- Patent DNA Extraction
Browse by: Latest US Patents, China's latest patents, Technical Efficacy Thesaurus, Application Domain, Technology Topic, Popular Technical Reports.
© 2024 PatSnap. All rights reserved.Legal|Privacy policy|Modern Slavery Act Transparency Statement|Sitemap|About US| Contact US: help@patsnap.com