Parallel multi-manipulator mechanism
A multi-operation, mobile phone technology, applied in the field of robotics, to achieve the effect of simple and compact structure
- Summary
- Abstract
- Description
- Claims
- Application Information
AI Technical Summary
Problems solved by technology
Method used
Image
Examples
Embodiment Construction
[0015] exist figure 1 In the schematic diagram of the parallel multi-operator mechanism shown, the machine base 1 is provided with a central concave spherical through-hole and 4 circumferentially uniformly distributed ball sub-seats, the moving table 2 is provided with a central through-hole and 4 circumferentially uniformly distributed ball sub-seats, and 4 Two SPS-type linear drive branches with the same structure are evenly distributed on the circumference between the machine base and the moving table, and the two ends of the SPS-type linear drive branch 3 are connected with the machine base and the moving table; Center, the set includes a heart tube 7, an inner sleeve 8, a fixed sleeve 9, an outer sleeve 10 and a ball sleeve 11, the heart tube and the inner sleeve, the inner sleeve and the fixed sleeve, the fixed sleeve and the outer sleeve, and the outer sleeve and the ball sleeve from the inside One end of the fixed sleeve is vertically fixed to the outer periphery of th...
PUM
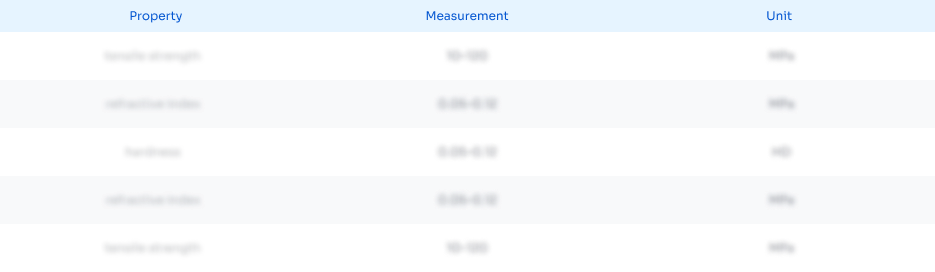
Abstract
Description
Claims
Application Information

- R&D
- Intellectual Property
- Life Sciences
- Materials
- Tech Scout
- Unparalleled Data Quality
- Higher Quality Content
- 60% Fewer Hallucinations
Browse by: Latest US Patents, China's latest patents, Technical Efficacy Thesaurus, Application Domain, Technology Topic, Popular Technical Reports.
© 2025 PatSnap. All rights reserved.Legal|Privacy policy|Modern Slavery Act Transparency Statement|Sitemap|About US| Contact US: help@patsnap.com