316 titanium fluidized bed drying-cooling process applied to potassium salt
A fluidized bed drying and fluidized bed cooling technology is applied in the directions of drying solid materials, drying gas arrangement, heating to dry solid materials, etc., and can solve the problems of agglomeration of potassium salt products, long drying time and high energy consumption, etc. Achieve the effect of reducing agglomeration, small product particle size and uniform heating
- Summary
- Abstract
- Description
- Claims
- Application Information
AI Technical Summary
Problems solved by technology
Method used
Image
Examples
Embodiment 1
[0027] 1) First-level drying, feed hot flue gas into the dryer until the cold air in the dryer is exhausted, send the potassium salt wet material into the dryer, and at the same time, feed the anti-caking powder with a liquid mass fraction of 1%. The agent is sprayed to the drier for 30min at a rate of 30min / L with a spray gun, and the potassium salt wet material is fully mixed with the anti-caking agent in the drying oven, and dried to form the first potassium salt dust; 2) Secondary drying, the air inlet temperature of the secondary drying is 400°C, the first potassium salt dust is evenly divided into three batches and rotated and sprayed in successively from the material inlet located on the upper part of the drying section of the 316 titanium fluidized bed, and two adjacent batches The interval time between them is 10min, and the hot flue gas is pressurized once between the two batches of spraying to keep the first potassium salt dust in boiling contact with the hot flue ga...
Embodiment 2
[0030]1) First-level drying, feed hot flue gas into the dryer until the cold air in the dryer is exhausted, send the potassium salt wet material into the dryer, and at the same time, feed the anti-caking powder with a liquid mass fraction of 1%. The agent is sprayed to the drier for 30min at a rate of 30min / L with a spray gun, and the potassium salt wet material is fully mixed with the anti-caking agent in the drying oven, and dried to form the first potassium salt dust; 2) Secondary drying, the air inlet temperature of the secondary drying is 425°C, the first potassium salt dust is evenly divided into three batches and rotated and sprayed in successively from the material inlet located on the upper part of the drying section of the 316 titanium fluidized bed, and two adjacent batches The interval time between them is 10min, and the hot flue gas is pressurized once between the two batches of spraying to keep the first potassium salt dust in boiling contact with the hot flue gas...
Embodiment 3
[0033] 1) First-level drying, feed hot flue gas into the dryer until the cold air in the dryer is exhausted, send the potassium salt wet material into the dryer, and at the same time, feed the anti-caking powder with a liquid mass fraction of 1%. The agent is sprayed to the drier for 30min at a rate of 30min / L with a spray gun, and the potassium salt wet material is fully mixed with the anti-caking agent in the drying oven, and dried to form the first potassium salt dust; 2) Secondary drying, the air inlet temperature of the secondary drying is 450°C, the first potassium salt dust is evenly divided into three batches and rotated and sprayed in successively from the material inlet located at the upper part of the drying section of the 316 titanium fluidized bed, and two adjacent batches The interval time between them is 10min, and the hot flue gas is pressurized once between the two batches of spraying to keep the first potassium salt dust in boiling contact with the hot flue ga...
PUM
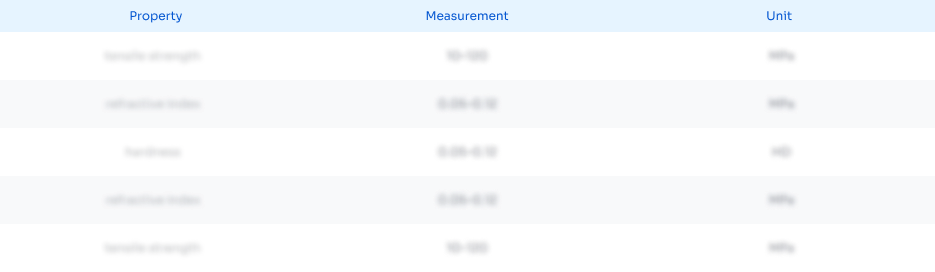
Abstract
Description
Claims
Application Information

- R&D Engineer
- R&D Manager
- IP Professional
- Industry Leading Data Capabilities
- Powerful AI technology
- Patent DNA Extraction
Browse by: Latest US Patents, China's latest patents, Technical Efficacy Thesaurus, Application Domain, Technology Topic, Popular Technical Reports.
© 2024 PatSnap. All rights reserved.Legal|Privacy policy|Modern Slavery Act Transparency Statement|Sitemap|About US| Contact US: help@patsnap.com