Treatment method for prolonging fatigue life of welding part
A fatigue life and treatment method technology, applied in the field of weldments, can solve problems such as unstable energy output, unqualified products, and poor stability of ultrasonic impact performance, so as to reduce the probability of fatigue crack growth, increase fatigue life, and improve the effect Effect
- Summary
- Abstract
- Description
- Claims
- Application Information
AI Technical Summary
Problems solved by technology
Method used
Image
Examples
Embodiment 1
[0019] A treatment method for improving the fatigue life of welded parts, comprising the following steps:
[0020] (1) Preheating treatment: preheat the weldment in a resistance furnace under nitrogen protection, and the preheating temperature is 320-350°C;
[0021] (2) The first ultrasonic shock treatment: the welded parts preheated in step (1) are subjected to the first ultrasonic shock treatment under a magnetic field of 20T, and the number of ultrasonic treatments is 2500 times / mm²;
[0022] (3) Irradiation treatment: Use the high-current pulsed ion beam composed of mixed ion beams to irradiate the welded parts treated in step (2). The number of irradiations is 5 times, and the irradiation time is 3-6s each time. The time interval is 1.5min;
[0023] (4) The second ultrasonic impact treatment: The welded parts treated in step (3) are subjected to the second ultrasonic impact treatment under a magnetic field of 50T, and the number of ultrasonic treatments is 35000 times / mm...
Embodiment 2
[0032] A treatment method for improving the fatigue life of welded parts, comprising the following steps:
[0033] (1) Preheating treatment: preheat the weldment in a resistance furnace under nitrogen protection, and the preheating temperature is 320-350°C;
[0034] (2) The first ultrasonic shock treatment: the welded parts preheated in step (1) are subjected to the first ultrasonic shock treatment under a magnetic field of 20T, and the number of ultrasonic treatments is 2500 times / mm²;
[0035] (3) Irradiation treatment: Use the high-current pulsed ion beam composed of mixed ion beams to irradiate the welded parts treated in step (2). The number of irradiations is 5 times, and the irradiation time is 3-6s each time. The time interval is 1.5min;
[0036] (4) The second ultrasonic impact treatment: The welded parts treated in step (3) are subjected to the second ultrasonic impact treatment under a magnetic field of 50T, and the number of ultrasonic treatments is 35000 times / mm...
Embodiment 3
[0045] A treatment method for improving the fatigue life of welded parts, comprising the following steps:
[0046] (1) Preheating treatment: preheat the weldment in a resistance furnace under nitrogen protection, and the preheating temperature is 320-350°C;
[0047] (2) The first ultrasonic shock treatment: the welded parts preheated in step (1) are subjected to the first ultrasonic shock treatment under a magnetic field of 20T, and the number of ultrasonic treatments is 2500 times / mm²;
[0048] (3) Irradiation treatment: Use the high-current pulsed ion beam composed of mixed ion beams to irradiate the welded parts treated in step (2). The number of irradiations is 5 times, and the irradiation time is 3-6s each time. The time interval is 1.5min;
[0049] (4) The second ultrasonic impact treatment: The welded parts treated in step (3) are subjected to the second ultrasonic impact treatment under a magnetic field of 50T, and the number of ultrasonic treatments is 35000 times / mm...
PUM
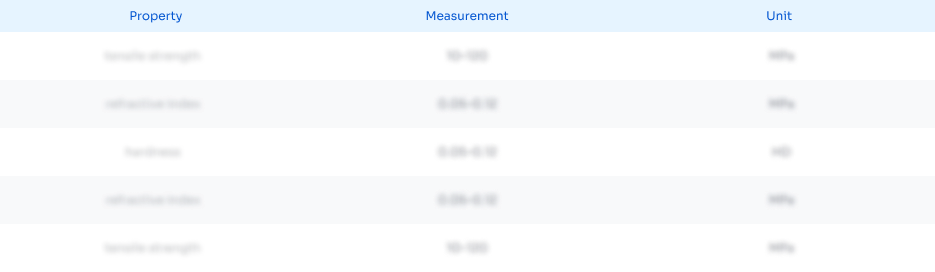
Abstract
Description
Claims
Application Information

- R&D Engineer
- R&D Manager
- IP Professional
- Industry Leading Data Capabilities
- Powerful AI technology
- Patent DNA Extraction
Browse by: Latest US Patents, China's latest patents, Technical Efficacy Thesaurus, Application Domain, Technology Topic, Popular Technical Reports.
© 2024 PatSnap. All rights reserved.Legal|Privacy policy|Modern Slavery Act Transparency Statement|Sitemap|About US| Contact US: help@patsnap.com