High-speed video measurement method for progressive collapse of latticed shell structure
A technology of video measurement and reticulated shell, which is applied in the field of civil engineering, can solve the problems of the influence of experimental results, the limited range of contact displacement measurement, and the inability to accurately measure spatial displacement results, etc.
- Summary
- Abstract
- Description
- Claims
- Application Information
AI Technical Summary
Problems solved by technology
Method used
Image
Examples
Embodiment
[0041] 1. Experiment introduction
[0042] The single-layer reticulated shell structure model is as follows figure 1 shown. This model is the most common Kewitte reticulated shell, and its internal force will be evenly distributed at each spherical node and member. In view of the limitations of the experimental environment, manufacturing process, and mechanical conditions, the diameter of the reticulated shell model is designed to be 4.2m. The model consists of 37 welded nodal balls and 132 connecting rods, and these welded nodal balls with a diameter of 60 mm are used to connect rods and counterweights. At the beginning of the experiment, the rupture of the reticulated shell will trigger the continuous collapse of the entire structure. In the process of its collapse, it is necessary to accurately measure the center displacement of each welded node sphere. Therefore, this paper designs a special artificial marker and related analysis algorithm to solve the above-mentioned ...
PUM
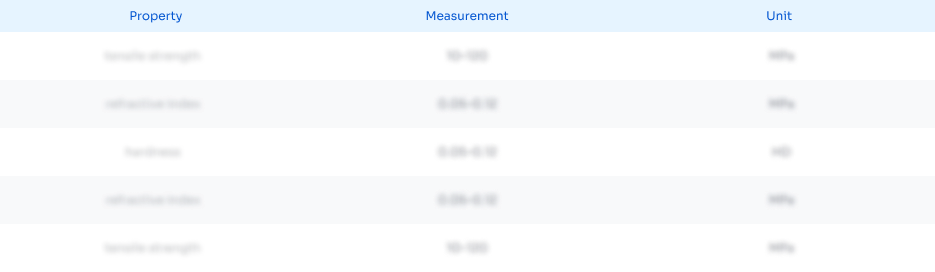
Abstract
Description
Claims
Application Information

- R&D
- Intellectual Property
- Life Sciences
- Materials
- Tech Scout
- Unparalleled Data Quality
- Higher Quality Content
- 60% Fewer Hallucinations
Browse by: Latest US Patents, China's latest patents, Technical Efficacy Thesaurus, Application Domain, Technology Topic, Popular Technical Reports.
© 2025 PatSnap. All rights reserved.Legal|Privacy policy|Modern Slavery Act Transparency Statement|Sitemap|About US| Contact US: help@patsnap.com