Magnesium alloy refiner and preparing method thereof
A refiner and magnesium alloy technology, applied in the field of magnesium alloys, can solve problems such as environmental pollution, poor refiner refinement effect, and influence on alloy corrosion resistance, so as to increase the nucleation rate and increase the nucleation rate , reducing the effect of nucleation work
- Summary
- Abstract
- Description
- Claims
- Application Information
AI Technical Summary
Problems solved by technology
Method used
Image
Examples
example 1
[0024] Weigh 950g of magnesium-aluminum alloy, 230g of carbon and manganese raw materials, and 0.5g of rare earth compound, add the magnesium-aluminum alloy into the melting furnace, and continuously feed the mixed gas of sulfur hexafluoride and nitrogen mixed at a volume ratio of 1:99 into the furnace Exhaust the air inside, then heat the melting furnace to 900°C, heat-preserve and smelt for 60 minutes to obtain a magnesium-aluminum melt, add rare earth compounds into the magnesium-aluminum melt, keep stirring at 150r / min for 15 minutes, then add carbon and manganese raw materials, and continue to keep warm Stir for 50 minutes to obtain the alloy melt, pour the alloy melt into shape, and add a low-voltage pulse magnetic field to the outside, start the pulse magnetic field generator immediately after casting, control the voltage to 300V, and the pulse frequency to 20Hz, so that the alloy melt is in the pulse magnetic field Solidify under the action, and turn off the pulse magne...
example 2
[0026] Weigh 600g of magnesium-aluminum alloy, 115g of carbon and manganese raw materials, and 0.2g of rare earth compounds, add the magnesium-aluminum alloy into the melting furnace, and continuously feed the mixed gas of sulfur hexafluoride and nitrogen mixed at a volume ratio of 1:99 into the furnace Exhaust the air inside, then heat the melting furnace to 750°C, heat-preserve and smelt for 40 minutes to obtain a magnesium-aluminum melt, add rare earth compounds into the magnesium-aluminum melt, keep stirring at 100r / min for 10 minutes, then add carbon and manganese raw materials, and continue to keep warm Stir for 30 minutes to obtain the alloy melt, pour the alloy melt into shape, and add a low-voltage pulse magnetic field to the outside, start the pulse magnetic field generator immediately after casting, control the voltage to 100V, and the pulse frequency to 5Hz, so that the alloy melt is in the pulsed magnetic field Solidify under the action, and turn off the pulse magn...
example 3
[0028] Weigh 800g of magnesium-aluminum alloy, 210g of carbon and manganese raw materials, and 0.3g of rare earth compounds, add the magnesium-aluminum alloy into the melting furnace, and continuously feed the mixed gas of sulfur hexafluoride and nitrogen mixed at a volume ratio of 1:99 into the furnace Exhaust the air inside, then heat the melting furnace to 800°C, heat-preserve and smelt for 50 minutes to obtain a magnesium-aluminum melt, add rare earth compounds into the magnesium-aluminum melt, keep stirring at 120r / min for 12 minutes, then add carbon and manganese raw materials, and continue to keep warm Stir for 40 minutes to obtain the alloy melt, pour the alloy melt into shape, and add a low-voltage pulse magnetic field outside, start the pulse magnetic field generating device immediately after casting, control the voltage to 200V, and the pulse frequency is 10Hz, so that the alloy melt is in the pulse magnetic field Solidify under the action, and turn off the pulse mag...
PUM
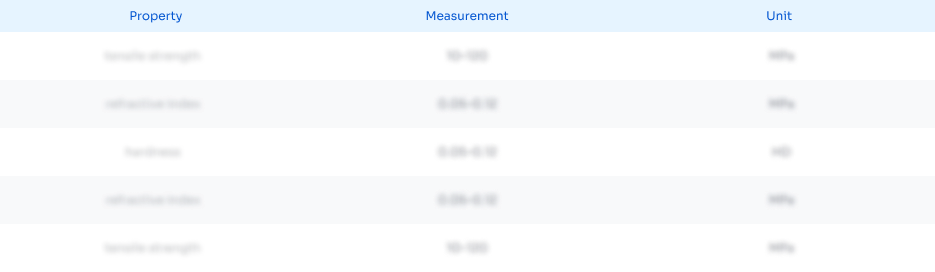
Abstract
Description
Claims
Application Information

- R&D
- Intellectual Property
- Life Sciences
- Materials
- Tech Scout
- Unparalleled Data Quality
- Higher Quality Content
- 60% Fewer Hallucinations
Browse by: Latest US Patents, China's latest patents, Technical Efficacy Thesaurus, Application Domain, Technology Topic, Popular Technical Reports.
© 2025 PatSnap. All rights reserved.Legal|Privacy policy|Modern Slavery Act Transparency Statement|Sitemap|About US| Contact US: help@patsnap.com