Intensity testing device for cooling fin
A technology of strength testing and cooling fins, which is applied in the direction of measuring devices, strength characteristics, and the use of stable torsion to test the strength of materials, etc., can solve problems such as loss, cooling fins affecting installation and normal use, and breakage to achieve accurate output Effect
- Summary
- Abstract
- Description
- Claims
- Application Information
AI Technical Summary
Problems solved by technology
Method used
Image
Examples
Embodiment Construction
[0020] The present invention will be further described below in conjunction with drawings and embodiments.
[0021] Such as Figure 1 to Figure 2 As shown, a heat sink 18 strength testing device includes a chassis 1, a limit block 2, a driving turntable 3, a first rotating shaft 4, a first coupling 5, a torque sensor 6, a second coupling 7, The second rotating shaft 8, the reducer 9, the motor 10 and the sliding device; the lower end of the underframe 1 is fixedly connected with a column 11, and the top end of the underframe 1 is fixedly connected with a limit block 2, and the end surface of the limit block 2 is provided with a The first strip-shaped groove 12, the second strip-shaped groove 13 is arranged on the driving turntable 3, the first groove 12 is directly opposite to the second groove 13, and the driving turntable 3 and the first rotating shaft 4 Coaxial connection, one end of the first rotating shaft 4 and the torque sensor 6 is coaxially fixed through the first co...
PUM
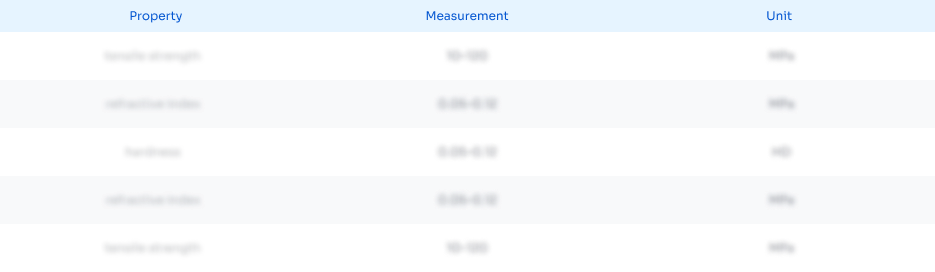
Abstract
Description
Claims
Application Information

- R&D
- Intellectual Property
- Life Sciences
- Materials
- Tech Scout
- Unparalleled Data Quality
- Higher Quality Content
- 60% Fewer Hallucinations
Browse by: Latest US Patents, China's latest patents, Technical Efficacy Thesaurus, Application Domain, Technology Topic, Popular Technical Reports.
© 2025 PatSnap. All rights reserved.Legal|Privacy policy|Modern Slavery Act Transparency Statement|Sitemap|About US| Contact US: help@patsnap.com