Strip steel rust removal technology
A strip steel and process technology, applied in the field of strip steel derusting technology, can solve the problems of complex structure of derusting equipment, unsatisfactory derusting effect, large loss of strip steel, etc., achieve good derusting effect and reduce waste acid discharge , high work efficiency
- Summary
- Abstract
- Description
- Claims
- Application Information
AI Technical Summary
Problems solved by technology
Method used
Image
Examples
Embodiment 1
[0025] like figure 1 Shown a kind of steel strip derusting process, comprises the steps:
[0026] a: Fix the strip steel on the transmission roller 2, and input it to the pretreatment pool 4 of the derusting box 1 under the action of the transmission system 3. The solution in the pretreatment pool 4 is a peeling agent, and the transmission roller 2 drives The strip steel rotates in full contact with the peeling agent to loosen the scale of the strip steel and pretreat the surface of the strip steel. The action of the driving roller 2 is driven by the first driving cylinder 5 installed on the derusting box 1;
[0027] b: The steel strip pretreated in step a is continuously conveyed to the brush device 6 for brushing rust. The brush device 6 includes the first brush roller 7 and the second brush roller 8 arranged in sequence, and the first brush roller 7 and the second brush roller 8 are placed directly above the strip to face the strip, and are driven by the second drive cylin...
Embodiment 2
[0031] like figure 1 Shown a kind of steel strip derusting process, comprises the steps:
[0032] a: Fix the strip steel on the transmission roller 2, and input it to the pretreatment pool 4 of the derusting box 1 under the action of the transmission system 3. The solution in the pretreatment pool 4 is a peeling agent, and the transmission roller 2 drives The strip steel rotates in full contact with the peeling agent to loosen the scale of the strip steel and pretreat the surface of the strip steel. The action of the driving roller 2 is driven by the first driving cylinder 5 installed on the derusting box 1;
[0033] b: The steel strip pretreated in step a is continuously conveyed to the brush device 6 for brushing rust. The brush device 6 includes the first brush roller 7 and the second brush roller 8 arranged in sequence, and the first brush roller 7 and the second brush roller 8 are placed directly above the strip to face the strip, and are driven by the second drive cylin...
Embodiment 3
[0037] like figure 1 Shown a kind of steel strip derusting process, comprises the steps:
[0038] a: Fix the strip steel on the transmission roller 2, and input it to the pretreatment pool 4 of the derusting box 1 under the action of the transmission system 3. The solution in the pretreatment pool 4 is a peeling agent, and the transmission roller 2 drives The strip steel rotates in full contact with the peeling agent to loosen the scale of the strip steel and pretreat the surface of the strip steel. The action of the driving roller 2 is driven by the first driving cylinder 5 installed on the derusting box 1;
[0039] b: The steel strip pretreated in step a is continuously conveyed to the brush device 6 for brushing rust. The brush device 6 includes the first brush roller 7 and the second brush roller 8 arranged in sequence, and the first brush roller 7 and the second brush roller 8 are placed directly above the strip to face the strip, and are driven by the second drive cylin...
PUM
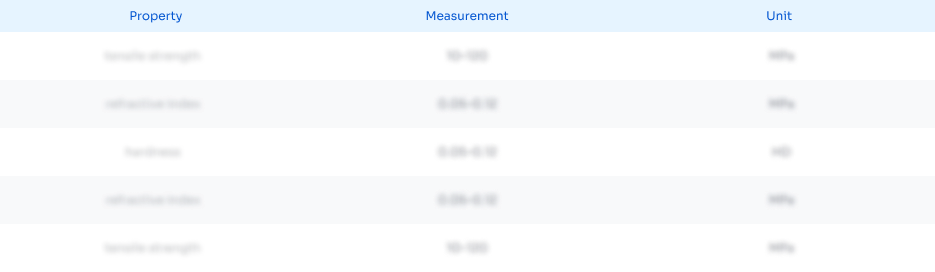
Abstract
Description
Claims
Application Information

- R&D
- Intellectual Property
- Life Sciences
- Materials
- Tech Scout
- Unparalleled Data Quality
- Higher Quality Content
- 60% Fewer Hallucinations
Browse by: Latest US Patents, China's latest patents, Technical Efficacy Thesaurus, Application Domain, Technology Topic, Popular Technical Reports.
© 2025 PatSnap. All rights reserved.Legal|Privacy policy|Modern Slavery Act Transparency Statement|Sitemap|About US| Contact US: help@patsnap.com