Stepped milling cutter
A milling cutter and step technology, applied in the field of step milling cutters, can solve the problems of surface quality not meeting the processing requirements, high production costs, low processing efficiency, etc., to reduce the risk of blade breakage, save processing time and tool setting. The effect of time and blade strength enhancement
- Summary
- Abstract
- Description
- Claims
- Application Information
AI Technical Summary
Problems solved by technology
Method used
Image
Examples
Embodiment Construction
[0028] The present invention will be described in further detail below in conjunction with the accompanying drawings and specific embodiments.
[0029] Figure 1 to Figure 4 An embodiment of the stepped milling cutter of the present invention is shown, the stepped milling cutter comprises a tool holder 2 and a cutting part 1, the cutting part 1 comprises four main edges and four helical flutes 14, each main edge is provided with a step Edge 13, the diameter of one pair of main blades in the four main blades is greater than the diameter of the other pair of main blades, and the main blade with a large diameter is the first peripheral blade 11, the small diameter of the main blade is the second peripheral blade 12, the first The length of the peripheral cutting edge 11 is greater than the length of the second peripheral cutting edge 12 . The outer diameter of the first peripheral cutting edge 11 is larger than that of the second peripheral cutting edge 12, in order to ensure th...
PUM
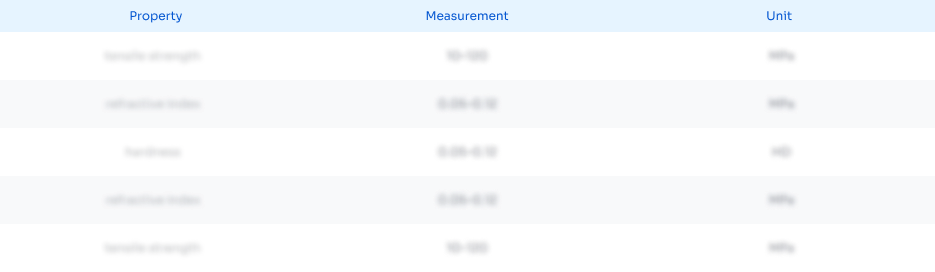
Abstract
Description
Claims
Application Information

- R&D Engineer
- R&D Manager
- IP Professional
- Industry Leading Data Capabilities
- Powerful AI technology
- Patent DNA Extraction
Browse by: Latest US Patents, China's latest patents, Technical Efficacy Thesaurus, Application Domain, Technology Topic, Popular Technical Reports.
© 2024 PatSnap. All rights reserved.Legal|Privacy policy|Modern Slavery Act Transparency Statement|Sitemap|About US| Contact US: help@patsnap.com