Catalyst components, catalyst systems and applications thereof for olefin polymerization
An olefin polymerization and catalyst technology, which is applied in the field of catalyst components for olefin polymerization, can solve the problems of narrow molecular weight distribution and high preparation cost of olefin polymers
- Summary
- Abstract
- Description
- Claims
- Application Information
AI Technical Summary
Problems solved by technology
Method used
Image
Examples
Embodiment 1
[0108] Take 10 g of the above-mentioned dialkoxymagnesium carrier, 50 mL of toluene, and 0.8 g of compound 1 to prepare a suspension. In a 300mL reaction kettle that has been repeatedly replaced with high-purity nitrogen, add 40mL of toluene and 60mL of titanium tetrachloride, raise the temperature to 65°C, then slowly add the prepared suspension into the kettle, keep the temperature at 65°C for 1 hour, and slowly raise the temperature to 110°C, when the temperature rises to 80°C, add 2.2g of compound 1, keep the temperature at 110°C for 1 hour, press filter to obtain a solid. The obtained solid was washed twice with 150 mL of toluene, and the liquid was removed by pressure filtration. A mixed solution of 90 mL of toluene and 60 mL of titanium tetrachloride was added and stirred at 110° C. for 1 hour, and treated twice in this way. Press filtration, wash the obtained solid once with toluene and 4 times with 150 mL of hexane, press filter and dry to obtain the catalyst solid c...
Embodiment 2-6
[0110] Using 3.0 g of compounds 2-6 as internal electron donors, the same preparation method as in Example 1 was used to prepare the catalyst solid component.
[0111] Method B:
[0112] (1) Configuration of alcoholate solution
[0113] In the reaction kettle that has been repeatedly replaced by high-purity nitrogen, 15.0g of anhydrous magnesium chloride, 60mL of toluene, and 63.5mL of isooctyl alcohol were sequentially added, and the reaction was carried out for 2.0 hours at a stirring speed of 300rpm and a temperature of 110°C to obtain a stable and uniform Alcohol solution. Add 0.8 mL of 3,5-heptanediol dibenzoate and 3.0 mL of diisobutyl phthalate, and react for 1.5 hours under the condition of stirring speed of 300 rpm and temperature of 110°C. Then 2.25 mL of tetrabutyl titanate was added, and the mixture was reacted for 1.5 hours at a stirring speed of 300 rpm and a temperature of 110° C. Then 90 mL of toluene was added, and the mixture was reacted for 0.5 hour at a ...
Embodiment 7
[0116] Add the above alcoholate solution into a reactor fully replaced by nitrogen and filled with 60mL of titanium tetrachloride and 40mL of toluene, and make them fully contact at -25°C for 1.5 hours by stirring, then raise the temperature to 110°C over 3 hours After constant temperature for 1 hour, add 108mL toluene and 12mL titanium tetrachloride, stir for 1 hour, cool and press filter, then add 12mL titanium tetrachloride and 108mL toluene, heat up to 100°C, add 1.5g compound 1, and keep constant temperature for 1 hour. Heat up to 110°C, add 72mL of toluene and 48mL of titanium tetrachloride and stir for 1 hour, press filter and wash the obtained solid once with 120mL of toluene and 4 times with 150mL of hexane. Press filter, transfer and dry to obtain the olefin polymerization catalyst component.
PUM
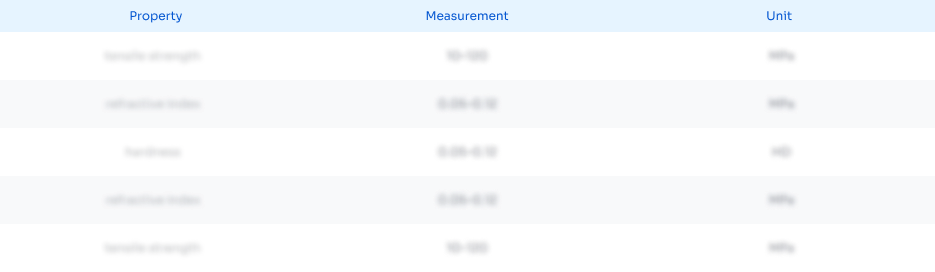
Abstract
Description
Claims
Application Information

- R&D
- Intellectual Property
- Life Sciences
- Materials
- Tech Scout
- Unparalleled Data Quality
- Higher Quality Content
- 60% Fewer Hallucinations
Browse by: Latest US Patents, China's latest patents, Technical Efficacy Thesaurus, Application Domain, Technology Topic, Popular Technical Reports.
© 2025 PatSnap. All rights reserved.Legal|Privacy policy|Modern Slavery Act Transparency Statement|Sitemap|About US| Contact US: help@patsnap.com