Production device for direct-pull winding composite glass reinforced plastic pipe
A glass steel pipe and production device technology, which is applied to tubular articles, other household appliances, household appliances, etc., can solve the problems of product failure and the quality of the pipe body, and achieve the effect of improving the composite quality, reducing the pulling resistance, and reducing the power consumption.
- Summary
- Abstract
- Description
- Claims
- Application Information
AI Technical Summary
Problems solved by technology
Method used
Image
Examples
Embodiment Construction
[0038] Referring to the accompanying drawings, a specific structure of the present invention is reflected. The production device of the Czochralski winding composite glass steel pipe includes a Czochralski layer unit 1, a forward winding layer unit 2, and a rewinding layer unit 3 which are sequentially distributed along the inner mold 7, and a set is arranged behind the rewinding layer unit 3. The outer mold 4 on the inner mold 7 is provided with a heating mechanism, and the rear of the outer mold 4 is sequentially distributed with a traction unit 5 and a cutting unit 6 . Inner mold 7 and outer mold 4 are all fixed. The traction unit 5 clamps and pulls the cured and formed pipe body 15 at the rear end, thereby driving the layers of glass fiber yarns at the front end to move backward. The cutting unit 6 cuts the solidified and formed pipe body 15 to length.
[0039] The CZ layer unit 1 includes several CZ layer yarn rolls 102 on the support 101, and the CZ layer glass fiber y...
PUM
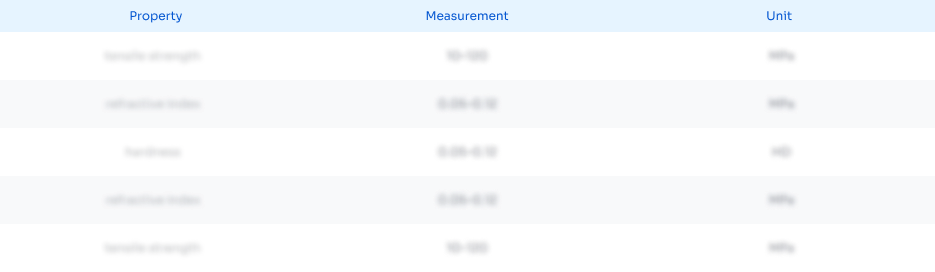
Abstract
Description
Claims
Application Information

- R&D
- Intellectual Property
- Life Sciences
- Materials
- Tech Scout
- Unparalleled Data Quality
- Higher Quality Content
- 60% Fewer Hallucinations
Browse by: Latest US Patents, China's latest patents, Technical Efficacy Thesaurus, Application Domain, Technology Topic, Popular Technical Reports.
© 2025 PatSnap. All rights reserved.Legal|Privacy policy|Modern Slavery Act Transparency Statement|Sitemap|About US| Contact US: help@patsnap.com