Three-layer composite water-absorption pad non-woven fabric and production method
A non-woven, layer-composite technology, applied in the field of non-woven manufacturing, can solve problems affecting product usability and hygiene, complex production process, complex structure, etc., achieve novel wear resistance, increase application fields, and ensure barrier. sexual effect
- Summary
- Abstract
- Description
- Claims
- Application Information
AI Technical Summary
Problems solved by technology
Method used
Image
Examples
Embodiment 1
[0020] Wet-laid pulp fiber layer: First, pulp cardboard and different long fibers are added to the material tank according to a predetermined ratio of 8:2 and mixed thoroughly, and the mixed solution is input into the conical pulp distributor through the pulp pump, and then The fiber net is formed on the forming net curtain, and the fiber net is rapidly dehydrated under the action of negative pressure suction to form a pulp fiber net with initial strength. The speed of pulp wet forming is 80:160m / min, the pressure of forming head is 45bar, and the pressure value of negative pressure suction box is 65%.
[0021] Polypropylene spunbond cloth layer: Polypropylene long fibers are made by electrostatic separation process. The raw materials are sucked into the hopper by the vacuum pump and fed into the screw extruder. After being extruded by the screw, the raw materials are accurately added to the spinning In the wire box, after spinning, after cooling, drawing, electrostatic separa...
Embodiment 2
[0025] Wet-laid pulp fiber layer: firstly, pulp cardboard is added to the material tank according to the proportion of 100% and fully mixed, and the mixed liquid is input into the conical pulper through the pulping pump, and the fiber web is formed on the forming screen curtain , The fiber web is rapidly dehydrated under the action of negative pressure suction to form a pulp fiber web with initial strength. The speed of pulp wet forming is 160m / min, the pressure of forming head is 45bar, and the pressure value of negative pressure suction box is 65%.
[0026] Polypropylene spunbond cloth layer: Polypropylene long fibers are made by electrostatic separation process. The raw materials are sucked into the hopper by the vacuum pump and fed into the screw extruder. After being extruded by the screw, the raw materials are accurately added to the spinning In the wire box, after spinning, after cooling, drawing, electrostatic separation and other processes, the final forming mesh curt...
PUM
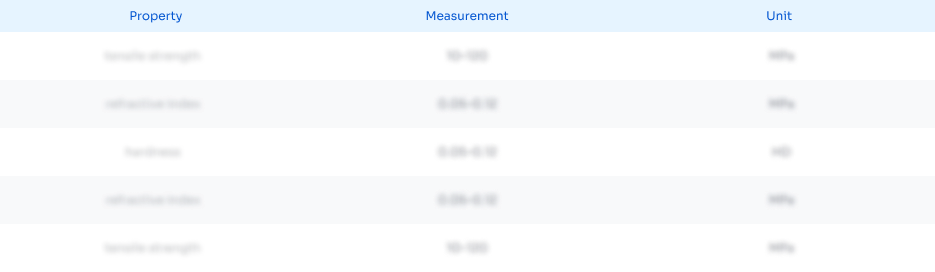
Abstract
Description
Claims
Application Information

- R&D Engineer
- R&D Manager
- IP Professional
- Industry Leading Data Capabilities
- Powerful AI technology
- Patent DNA Extraction
Browse by: Latest US Patents, China's latest patents, Technical Efficacy Thesaurus, Application Domain, Technology Topic, Popular Technical Reports.
© 2024 PatSnap. All rights reserved.Legal|Privacy policy|Modern Slavery Act Transparency Statement|Sitemap|About US| Contact US: help@patsnap.com