A Method for Measuring Transverse Space Vibration of Wire Rope
A technology of vibration measurement and steel wire rope, which is applied in the direction of measuring devices, measuring ultrasonic/sonic/infrasonic waves, instruments, etc. It can solve the problems of difficult implementation, inability to guarantee measurement accuracy, adding laser sensors, etc., and achieve the effect of simple operation mode
- Summary
- Abstract
- Description
- Claims
- Application Information
AI Technical Summary
Problems solved by technology
Method used
Image
Examples
Embodiment Construction
[0023] The following will clearly and completely describe the technical solutions in the embodiments of the present invention with reference to the accompanying drawings in the embodiments of the present invention. Obviously, the described embodiments are only some, not all, embodiments of the present invention. Based on the embodiments of the present invention, all other embodiments obtained by persons of ordinary skill in the art without making creative efforts belong to the protection scope of the present invention.
[0024] see Figure 1-4 Shown: Taking the horizontal space vibration detection of the steel wire rope between the winding hoist drum and the sky wheel as an example, as shown in Figure 4 As shown, 1 is the hoist drum, 2 is the wire rope between the hoist drum and the hoisting sky wheel, 3 is the sky wheel, and 4 is the lifting load, so what needs to be detected is the distance between the hoist drum 1 and the sky wheel 3. Horizontal spatial vibration, establi...
PUM
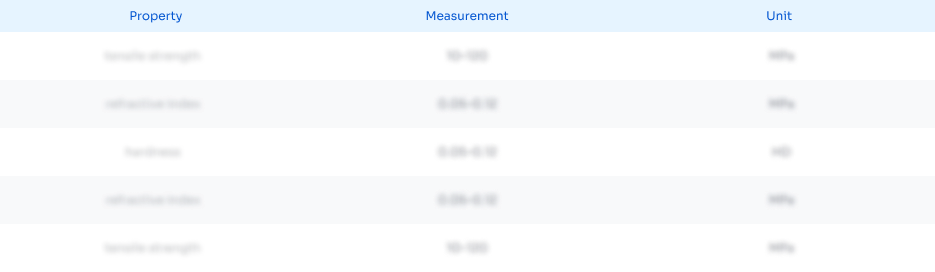
Abstract
Description
Claims
Application Information

- Generate Ideas
- Intellectual Property
- Life Sciences
- Materials
- Tech Scout
- Unparalleled Data Quality
- Higher Quality Content
- 60% Fewer Hallucinations
Browse by: Latest US Patents, China's latest patents, Technical Efficacy Thesaurus, Application Domain, Technology Topic, Popular Technical Reports.
© 2025 PatSnap. All rights reserved.Legal|Privacy policy|Modern Slavery Act Transparency Statement|Sitemap|About US| Contact US: help@patsnap.com