An offset press UV varnishing method
A technology for offset printing presses and printing plates, which is applied to general parts of printing machinery, printing presses, printing and other directions, can solve the problems of inability to print three-dimensional effects and complicated processes, and achieves easy follow-up processing, low cost, and convenient and fast manufacturing. Effect
- Summary
- Abstract
- Description
- Claims
- Application Information
AI Technical Summary
Problems solved by technology
Method used
Examples
Embodiment 1
[0028] A method for UV glazing of an offset printing machine, comprising the steps of:
[0029] 1) Select the liner paper and the original: choose the liner paper with a thickness of 0.2-0.3mm; select the original that needs to design a concave-convex three-dimensional pattern;
[0030] 2) cutting off the area of the liner paper corresponding to the non-image part in the printed matter to form a hollow, leaving the printed area;
[0031] 3) Install the color sequence printing plate;
[0032] 4) Lay the cut backing paper flat on the printing area on the blanket, and then install the backing paper together with the blanket on the blanket cylinder and fix and lock it;
[0033] 5) Light ink setting;
[0034] 6) UV light setting: turn on the UV light in the offset printing machine; at least one UV light is set between every two color groups, and the UV light must be set at the position corresponding to the last color group in the printing process;
[0035] 7) Adjust the offset...
Embodiment 2
[0039] A method for UV glazing of an offset printing machine, comprising the steps of:
[0040] 1) Select the liner paper and the original: select the liner paper with a thickness of 0.2-0.3mm; select the original that needs to design a concave-convex three-dimensional pattern; set the color value at the position of the pattern that needs a matte effect in the original 100k, and set the color value to 0k for the remaining parts, so as to effectively distinguish the part that needs matte effect and the fish part of the original, which is convenient for subsequent processing.
[0041] 2) cutting off the area of the liner paper corresponding to the non-image part in the printed matter to form a hollow, leaving the printed area;
[0042] 3) Install the color sequence printing plate; use the CTP plate for UV printing to make the printing plate, and design the color sequence according to the color required for the concave-convex three-dimensional pattern in the original manuscript...
Embodiment 3
[0050] A method for UV glazing of an offset printing machine, comprising the steps of:
[0051] 1) Select the liner paper and the original: select the liner paper with a thickness of 0.2-0.3mm; select the original that needs to design a concave-convex three-dimensional pattern; set the color value at the position of the pattern that needs a matte effect in the original 100k, and set the color value to 0k for the remaining parts, so as to effectively distinguish the part that needs matte effect and the fish part of the original, which is convenient for subsequent processing.
[0052] 2) cutting off the area of the liner paper corresponding to the non-image part in the printed matter to form a hollow, leaving the printed area;
[0053] 3) Install the color sequence printing plate; use the CTP plate for UV printing to make the printing plate, and design the color sequence according to the color required for the concave-convex three-dimensional pattern in the original manuscript...
PUM
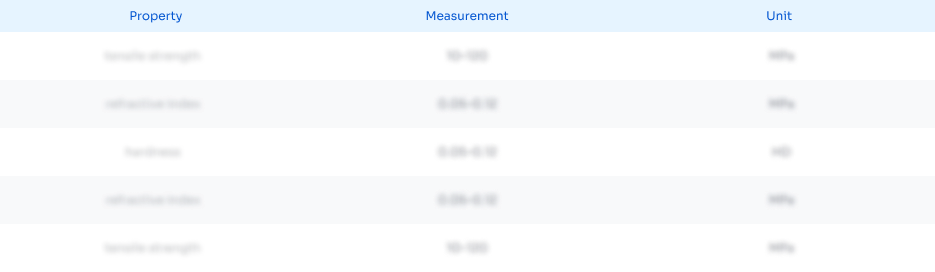
Abstract
Description
Claims
Application Information

- R&D
- Intellectual Property
- Life Sciences
- Materials
- Tech Scout
- Unparalleled Data Quality
- Higher Quality Content
- 60% Fewer Hallucinations
Browse by: Latest US Patents, China's latest patents, Technical Efficacy Thesaurus, Application Domain, Technology Topic, Popular Technical Reports.
© 2025 PatSnap. All rights reserved.Legal|Privacy policy|Modern Slavery Act Transparency Statement|Sitemap|About US| Contact US: help@patsnap.com