Light-weight, energy-saving and environment-friendly prefabricated floor slab and installation process thereof
An energy-saving, environmental-friendly, prefabricated panel technology, applied in the direction of floor slabs, building materials, building components, etc., can solve the problems of short construction period, low cost, high difficulty, etc., and achieve the effect of sound insulation and earthquake resistance, fast growth rate, and saving consumption.
- Summary
- Abstract
- Description
- Claims
- Application Information
AI Technical Summary
Problems solved by technology
Method used
Image
Examples
Embodiment Construction
[0029] Such as figure 1 , 2 , 3, shown in 4, the light weight, energy-saving and environment-friendly prefabricated floor slab of the present invention comprises bamboo layer 1 and the concrete layer 2 of wrapping bamboo layer, and bamboo layer is three layers, and each bamboo layer is made of several lengths equal and arranged in parallel The bamboo poles of each bamboo layer are tiled, and the distance between the bamboo poles of each bamboo layer and the bamboo poles is 5-10cm. The length direction of the bamboo poles between two adjacent bamboo layers is perpendicular to each other. The length directions of the boards are parallel, the adjacent bamboo poles of the same bamboo layer are arranged alternately by bamboo heads and bamboo tails, the gaps between the bamboo poles of the same layer and different layers are filled with concrete, and each bamboo pole 12 of the second bamboo layer is fixed with Bamboo stirrups 13, the bamboo stirrups surround each bamboo pole that i...
PUM
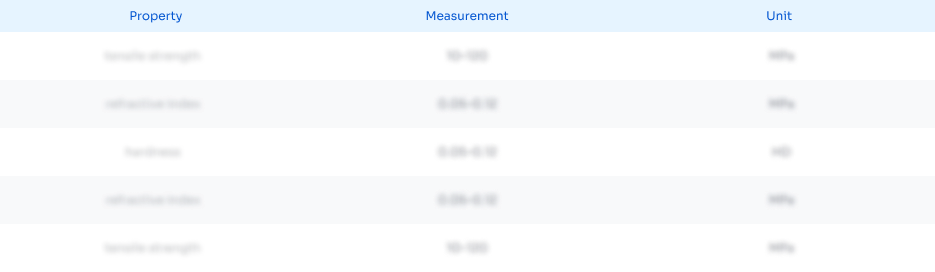
Abstract
Description
Claims
Application Information

- R&D
- Intellectual Property
- Life Sciences
- Materials
- Tech Scout
- Unparalleled Data Quality
- Higher Quality Content
- 60% Fewer Hallucinations
Browse by: Latest US Patents, China's latest patents, Technical Efficacy Thesaurus, Application Domain, Technology Topic, Popular Technical Reports.
© 2025 PatSnap. All rights reserved.Legal|Privacy policy|Modern Slavery Act Transparency Statement|Sitemap|About US| Contact US: help@patsnap.com