Driving control method for novel slewing bearing test bed
A technology of slewing bearings and test benches, applied in the direction of adaptive control, comprehensive factory control, general control system, etc., can solve problems such as difficulty in ensuring stable control of the system
- Summary
- Abstract
- Description
- Claims
- Application Information
AI Technical Summary
Problems solved by technology
Method used
Image
Examples
Embodiment Construction
[0079] The present invention will be further described below in conjunction with the accompanying drawings.
[0080] Such as Figures 1 to 9 , a new drive control method for a slewing bearing test bench, comprising the following steps:
[0081] Step (1) as figure 1 It shows the transfer function identification principle of the slewing ring control system. After the step input voltage signal is given, the position signal data is measured by the position sensor of the slewing ring;
[0082] Step (2) Set the expected step response trajectory of the slewing bearing according to the second-order system performance index. The standard second-order system response can be determined by the system damping ratio ξ and natural frequency ω n Calculations are performed where the natural frequency is obtained according to the 2% criterion:
[0083]
[0084] where T set It is the stabilization time of the system, which determines the response speed of the system from another angle. a...
PUM
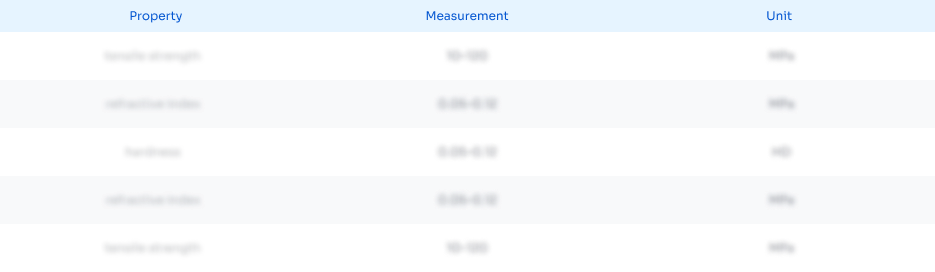
Abstract
Description
Claims
Application Information

- R&D Engineer
- R&D Manager
- IP Professional
- Industry Leading Data Capabilities
- Powerful AI technology
- Patent DNA Extraction
Browse by: Latest US Patents, China's latest patents, Technical Efficacy Thesaurus, Application Domain, Technology Topic, Popular Technical Reports.
© 2024 PatSnap. All rights reserved.Legal|Privacy policy|Modern Slavery Act Transparency Statement|Sitemap|About US| Contact US: help@patsnap.com