Method and device for identification of working mode parameters based on self-iterative principal component extraction
A technology for working mode and parameter identification, which is used in measurement devices, electrical digital data processing, special data processing applications, etc.
- Summary
- Abstract
- Description
- Claims
- Application Information
AI Technical Summary
Problems solved by technology
Method used
Image
Examples
Embodiment 1
[0119] Apply multi-frequency sinusoidal excitation to the undamped simply supported beam; divide the undamped simply supported beam with a length of 1 meter into 1000 equal parts, and generate 1001 response measuring points, m=1001; frequency sine excitation and obtain response data; the sampling frequency is 4096Hz, the sampling time is 1s, T=4096, set the accuracy threshold α=0.000001, the current order contribution threshold η=0.001, and the maximum number of iterations T max = 100;
[0120] Such as Figure 7 As shown, the modal coordinate response is obtained through the working modal parameter identification algorithm based on self-iterative principal component extraction, and the FFT calculation is performed on it to obtain the common frequency of each order;
[0121] Such as Figure 8 As shown, the comparison between the identified mode shape and the real mode shape shows that the working mode parameter identification method based on self-iterative principal component...
Embodiment 2
[0137] A cylindrical shell with simply supported boundary conditions at both ends is excited by uniform reverberation Gaussian white noise. The parameters of the cylindrical shell are: thickness 0.005m, length 0.37m, radius 0.1825m, elastic modulus 205GPa, material Poisson's ratio 0.3, material density 7850kg / m*m*m; the modal damping ratios are 0.03, 0.05, 0.10 respectively. 4370 sensors are evenly arranged on the surface, the sampling frequency is set to 5120Hz, and the sampling time is set to 1s. Using the finite element method in the LMS Virtual.lab software for calculation, the structural displacement response data in the X, Y, and Z directions of three different damping ratios are obtained from each observation point to form a response data set in the three directions
[0138] Such as Figure 10 As shown, the response signal matrix in three directions of the three-dimensional structure is observed, and the response signals in the three directions are directly assembled ...
Embodiment 3
[0153] Combining the short-term time-invariant theory and the self-iterative principal component extraction algorithm, the operating mode at each time is estimated by using the statistical characteristics of the operating mode parameter identification method of the linear time-varying structure based on the sliding window self-iterative principal component extraction in each window parameters (including the natural frequency and mode shape of each mode), and then the working mode parameters obtained at each time are connected to realize the identification of time-varying linear structural working mode parameters.
[0154] In this embodiment, the method for identifying working modal parameters of linear time-varying structures based on sliding window self-iterative principal component extraction uses a one-dimensional cantilever beam structure to simulate a time-varying structure. For a one-dimensional cantilever beam structure, without considering shear In the case of deformati...
PUM
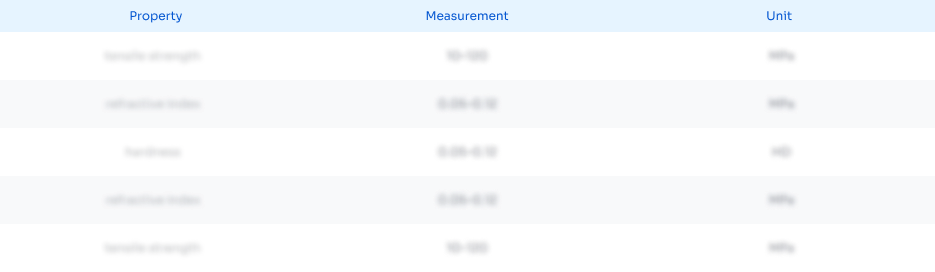
Abstract
Description
Claims
Application Information

- R&D
- Intellectual Property
- Life Sciences
- Materials
- Tech Scout
- Unparalleled Data Quality
- Higher Quality Content
- 60% Fewer Hallucinations
Browse by: Latest US Patents, China's latest patents, Technical Efficacy Thesaurus, Application Domain, Technology Topic, Popular Technical Reports.
© 2025 PatSnap. All rights reserved.Legal|Privacy policy|Modern Slavery Act Transparency Statement|Sitemap|About US| Contact US: help@patsnap.com