Environment-friendly foaming material for air inlet pipe assembly and preparation method
A foamed material and air intake pipe technology, applied in the automotive field, can solve the problems of hidden safety hazards, short escape time for personnel, poor flame retardancy, etc., and achieve the effects of reasonable collocation, high flame retardancy, and protection of vehicles and personal safety.
- Summary
- Abstract
- Description
- Claims
- Application Information
AI Technical Summary
Problems solved by technology
Method used
Examples
Embodiment 1
[0026] A method for preparing an environmentally friendly flame-retardant foaming material for an intake pipe assembly, comprising the following preparation steps:
[0027] (1) Raw material treatment: dry polyether 403, polyether 635 and isocyanate at a drying temperature of 40°C and a drying time of 6 hours;
[0028] (2) Weighing proportion: According to the mass proportion, weigh glass fiber: 150 parts, silicone oil: 1.5 parts, triethanolamine: 8 parts, catalyst A33: 1.2 parts, catalyst HP-30: 1.5 parts, water: 30 parts parts, flame retardant DMMP: 35 parts, and polyether 330: 30 parts, polyether 450: 35 parts, polyether 403: 15 parts after drying;
[0029] (3) Preparation of combined materials: Add the weighed polyether 330, polyether 450, polyether 403, glass fiber, silicone oil, triethanolamine, catalyst A33, catalyst HP-30, water and flame retardant into the reaction kettle in sequence Thoroughly stir, the stirring time is 0.5h, the stirring temperature is 50°C, and the...
Embodiment 2
[0032] A method for preparing an environmentally friendly flame-retardant foaming material for an intake pipe assembly, comprising the following preparation steps:
[0033] (1) Raw material treatment: dry polyether 330, polyether 450, polyether 403 and isocyanate at a drying temperature of 40°C and a drying time of 7 hours;
[0034] (2) Weighing ratio: According to the weight ratio, weigh glass fiber: 175 parts, silicone oil: 2 parts, triethanolamine: 10 parts, catalyst A33: 1.35 parts, catalyst HP-30: 1.65 parts, water: 35 parts parts, flame retardant DMMP: 37.5 parts, and polyether 330: 35 parts, polyether 450: 40 parts, polyether 403: 20 parts after drying;
[0035] (3) Preparation of combined materials: Add the weighed polyether 330, polyether 450, polyether 403, glass fiber, silicone oil, triethanolamine, catalyst A33, catalyst HP-30, water and flame retardant into the reaction kettle in sequence Thoroughly stir, the stirring time is 1h, the stirring temperature is 65°C,...
Embodiment 3
[0038] A method for preparing an environmentally friendly flame-retardant foaming material for an intake pipe assembly, comprising the following preparation steps:
[0039] (1) Raw material treatment: dry polyether 330, polyether 450, polyether 403 and isocyanate at a drying temperature of 40°C and a drying time of 8 hours;
[0040] (2) Weighing proportion: According to the mass proportion, weigh glass fiber: 200 parts, silicone oil: 2.5 parts, triethanolamine: 12 parts, catalyst A33: 1.5 parts, catalyst HP-30: 1.8 parts, water: 40 parts parts, flame retardant DMMP: 40 parts, and polyether 330: 40 parts, polyether 450: 45 parts, polyether 403: 25 parts after drying;
[0041] (3) Preparation of combined materials: Add the weighed polyether 330, polyether 450, polyether 403, glass fiber, silicone oil, triethanolamine, catalyst A33, catalyst HP-30, water and flame retardant into the reaction kettle in sequence Thoroughly stir, the stirring time is 1.5h, the stirring temperature ...
PUM
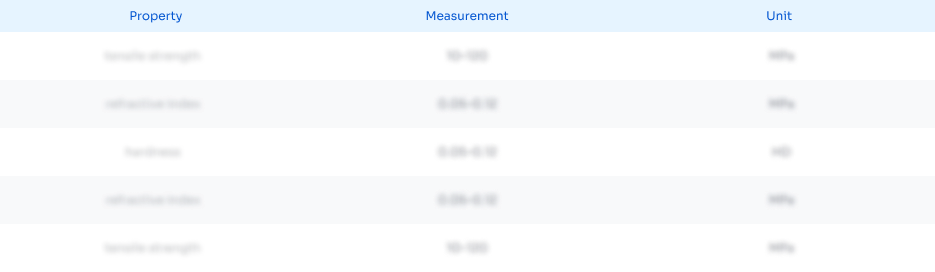
Abstract
Description
Claims
Application Information

- R&D
- Intellectual Property
- Life Sciences
- Materials
- Tech Scout
- Unparalleled Data Quality
- Higher Quality Content
- 60% Fewer Hallucinations
Browse by: Latest US Patents, China's latest patents, Technical Efficacy Thesaurus, Application Domain, Technology Topic, Popular Technical Reports.
© 2025 PatSnap. All rights reserved.Legal|Privacy policy|Modern Slavery Act Transparency Statement|Sitemap|About US| Contact US: help@patsnap.com