Vibration grinding machine based on double-machine coaxial self synchronism and parameter determining method
A dual-machine coaxial and grinding machine technology, which is applied to machine tools suitable for grinding the edge of workpieces, grinding machines, surface polishing machine tools, etc., can solve the problems of unloading need to stop, low energy utilization rate, etc., to improve production efficiency , Improve energy utilization, improve the effect of automation
- Summary
- Abstract
- Description
- Claims
- Application Information
AI Technical Summary
Problems solved by technology
Method used
Image
Examples
Embodiment Construction
[0182] A self-synchronized vibratory grinding based on dual-machine coaxial,. See figure 1 , including an upper vibrator 1, a vibration tank 2, a lining 3, a spring 4, a lower vibrator 5, a base 6 and a discharge port 7. It is characterized in that the base 6 is placed on the ground or foundation, the spring 4 is placed above the base 6, the vibration tank 2 is placed above the spring 4, the vibration tank 2 is provided with a discharge port 7, and the lining 3 is attached to the inner wall of the vibration tank 2, The upper vibrator 1 and the lower vibrator 5 are respectively composed of motor-driven eccentric rotors. The upper and lower vibrators are arranged symmetrically and coaxially. The upper vibrator 1 is placed above the vibration tank, and the lower vibrator 5 is placed in the vibration tank. The lower parts are all firmly connected with the vibrating tank. When the vibrating tank is full of materials, the phase angle of the upper and lower exciters is 0, and the ...
PUM
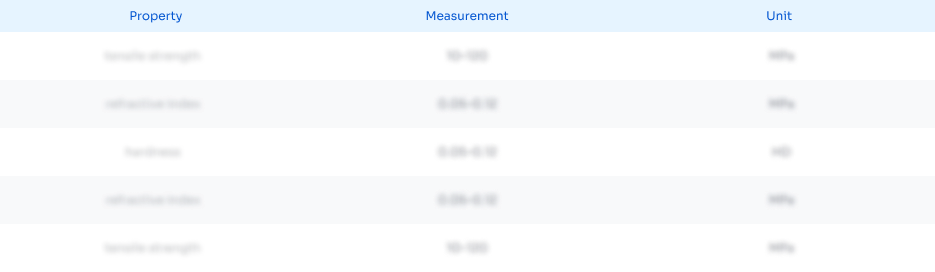
Abstract
Description
Claims
Application Information

- R&D Engineer
- R&D Manager
- IP Professional
- Industry Leading Data Capabilities
- Powerful AI technology
- Patent DNA Extraction
Browse by: Latest US Patents, China's latest patents, Technical Efficacy Thesaurus, Application Domain, Technology Topic, Popular Technical Reports.
© 2024 PatSnap. All rights reserved.Legal|Privacy policy|Modern Slavery Act Transparency Statement|Sitemap|About US| Contact US: help@patsnap.com