A Method of Suppressing Commutation Torque Ripple of Brushless DC Motor
A brushed DC motor, phase torque technology, applied in the direction of torque ripple control, electronic commutator, etc., can solve the problem of the delay of the Hall sensor detection position signal, the inconsistency of the turn-off phase current falling rate and the on-phase current rising rate, problems such as advance, to achieve the effect of suppressing commutation torque ripple, improving operating efficiency, and being easy to implement
- Summary
- Abstract
- Description
- Claims
- Application Information
AI Technical Summary
Problems solved by technology
Method used
Image
Examples
Embodiment
[0100] The specifications of the brushless DC motor used in the present invention are shown in Table 2:
[0101] Table 2. Motor Specifications and Parameters
[0102]
[0103] When the motor is running in the rated state, convert the parameters in the table to obtain the mechanical angular velocity of the motor Ω=50π(rad / s), the electrical angular velocity of the motor ω=200π(rad / s), the amplitude of the back electromotive force E=92.7V, and the phase current stable value I 0 =22A, electromagnetic torque T in steady state e = 26 Nm.
[0104] Substituting the parameters into formula (5) (3) to obtain the duty cycle D during the delay period d and off-phase current I 1 With delay angle θ d change curve, such as Figure 10 shown, the duty cycle D d If the delay is less than 1 within the 30° electrical angle range, the PWM duty cycle can be adjusted to ensure that the motor torque is constant during the delay; Figure 11 As shown, the turn-off phase current I 1 One-to-...
PUM
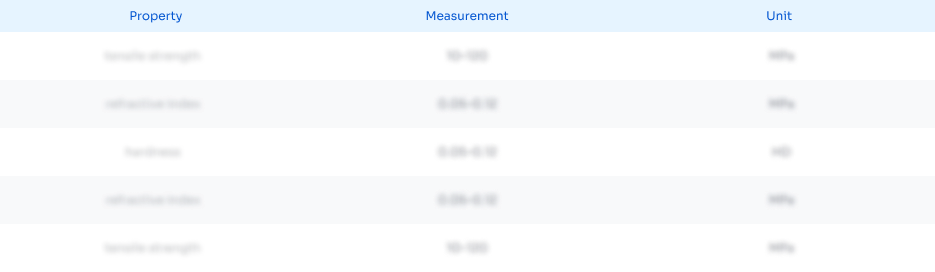
Abstract
Description
Claims
Application Information

- R&D Engineer
- R&D Manager
- IP Professional
- Industry Leading Data Capabilities
- Powerful AI technology
- Patent DNA Extraction
Browse by: Latest US Patents, China's latest patents, Technical Efficacy Thesaurus, Application Domain, Technology Topic, Popular Technical Reports.
© 2024 PatSnap. All rights reserved.Legal|Privacy policy|Modern Slavery Act Transparency Statement|Sitemap|About US| Contact US: help@patsnap.com