Technology for hot-melting edge cutting and splitting of mesh yarns, and device of same
A mesh and hot-melt technology, which is applied in the cutting of textile materials, textiles and papermaking, etc., can solve the problems of increasing product scrap rate, easy sticking and falling of filaments, so as to improve product quality and production progress, and reduce scrap The effect of appropriate rate and hardness
- Summary
- Abstract
- Description
- Claims
- Application Information
AI Technical Summary
Problems solved by technology
Method used
Image
Examples
Embodiment Construction
[0021] Specific embodiments of the present invention will be described below.
[0022] Such as Figure 2 to Figure 4 As shown, a hot-melt edge trimming and slitting device adopting a hot-melt edge trimming and slitting process includes a rotating shaft 10, which is sleeved on the first fixed sleeve plate 11, and one end of the rotating shaft 10 is connected to the rotating shaft connecting plate 12 The rotating shaft mounting hole 1201 opened on the top is matched, the rotating shaft connecting plate 12 is pinned to one end of the cylinder connecting plate 13, and the other end of the cylinder connecting plate 13 is connected to the output end of the cylinder 14; the second fixed sleeve plate is also sleeved on the rotating shaft 10 15. The second fixed sleeve plate 15 is connected to one end of the hot-melt knife fixed plate 16, and the other end of the hot-melt knife fixed plate 16 is provided with a hot-melt knife 17. The hot-melt knife 17 increases the temperature by elect...
PUM
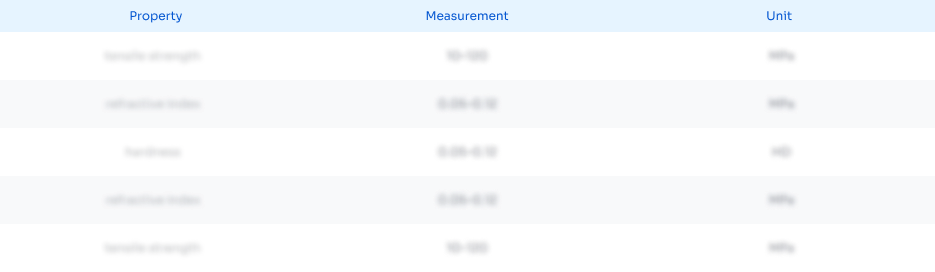
Abstract
Description
Claims
Application Information

- Generate Ideas
- Intellectual Property
- Life Sciences
- Materials
- Tech Scout
- Unparalleled Data Quality
- Higher Quality Content
- 60% Fewer Hallucinations
Browse by: Latest US Patents, China's latest patents, Technical Efficacy Thesaurus, Application Domain, Technology Topic, Popular Technical Reports.
© 2025 PatSnap. All rights reserved.Legal|Privacy policy|Modern Slavery Act Transparency Statement|Sitemap|About US| Contact US: help@patsnap.com