Tungsten oxide nano-belt structure electrochromic film preparation method
An electrochromic and nanobelt technology, applied in the direction of tungsten oxide/tungsten hydroxide, coatings, etc., can solve the problems of unsatisfactory electrochromic performance, hindering electrochromic electron transport, and complicated preparation process of seed layer, etc. Achieve the effect of improving electron transmission efficiency, improving electrochromic response speed, and shortening dispersion path
- Summary
- Abstract
- Description
- Claims
- Application Information
AI Technical Summary
Problems solved by technology
Method used
Image
Examples
Embodiment 1
[0029] Immerse the FTO conductive glass in deionized water and ultrasonically wash it for 15 minutes, dry it with nitrogen gas, and irradiate it under a UV lamp for 5 minutes before use. Weigh 0.3042g of paratungsine and 6.3g of oxalic acid dihydrate and dissolve them in 25mL of absolute ethanol, and obtain a reaction solution after ultrasonic oscillation; then transfer the reaction solution to a hydrothermal reaction kettle, and place the cleaned FTO conductive glass Invade into the hydrothermal kettle containing the reaction solution, in which the FTO conductive glass is placed obliquely with the conductive side facing down, and kept at 200 °C for 8 hours, and finally cooled to room temperature naturally, and the FTO conductive glass is taken out, washed with water and ethanol in sequence, and then dried. Then the obtained film was calcined at 400°C for 1.5 hours to obtain the electrochromic film with tungsten oxide nanoribbon structure. figure 1 For the X-ray diffraction pa...
Embodiment 2
[0032]Immerse the FTO conductive glass in deionized water and ultrasonically wash it for 20 minutes, blow it dry with nitrogen gas, and irradiate it under a UV lamp for 3 minutes before use. Weigh 0.3042g of paratungsine and 6.3g of oxalic acid dihydrate and dissolve them in 25mL of absolute ethanol, and obtain a reaction solution after ultrasonic oscillation; then transfer the reaction solution to a hydrothermal reaction kettle, and place the cleaned FTO conductive glass Invade into the hydrothermal kettle containing the reaction solution, in which the FTO conductive glass is placed obliquely with the conductive side facing down, and kept at 200°C for 4 hours, and finally cooled to room temperature naturally, and the FTO conductive glass is taken out, washed with water and ethanol in sequence, and then dried. Then the obtained film was calcined at 350° C. for 3 hours to obtain an electrochromic film with a tungsten oxide nanoribbon structure. Figure 6 It is a scanning electr...
Embodiment 3
[0034] Immerse the FTO conductive glass in deionized water and ultrasonically wash it for 30 minutes, dry it with nitrogen gas, and irradiate it under a UV lamp for 1 minute before use. Weigh 0.1521g of paratungsine and 6.3g of oxalic acid dihydrate, dissolve them in 25mL of absolute ethanol, and obtain a reaction solution after ultrasonic oscillation; then transfer the reaction solution to a hydrothermal reaction kettle, and place the cleaned FTO conductive glass Invade into the hydrothermal kettle containing the reaction solution, in which the FTO conductive glass is placed obliquely with the conductive side facing down, and kept at 180 °C for 12 hours, and finally cooled to room temperature naturally, the FTO conductive glass is taken out, washed with water and ethanol in sequence, and then dried. Then the obtained film was calcined at 500° C. for 1 hour to obtain an electrochromic film with a tungsten oxide nanoribbon structure. Figure 7 For the scanning electron microgra...
PUM
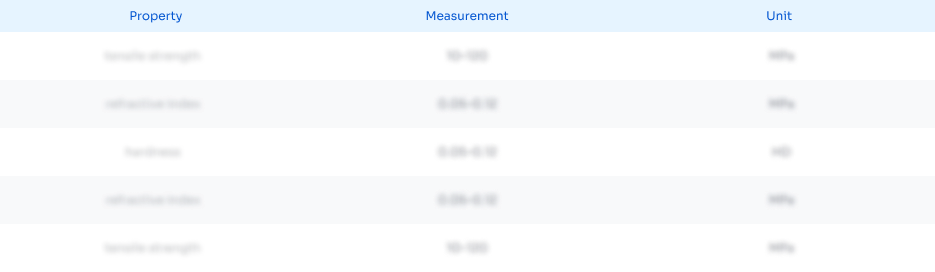
Abstract
Description
Claims
Application Information

- R&D
- Intellectual Property
- Life Sciences
- Materials
- Tech Scout
- Unparalleled Data Quality
- Higher Quality Content
- 60% Fewer Hallucinations
Browse by: Latest US Patents, China's latest patents, Technical Efficacy Thesaurus, Application Domain, Technology Topic, Popular Technical Reports.
© 2025 PatSnap. All rights reserved.Legal|Privacy policy|Modern Slavery Act Transparency Statement|Sitemap|About US| Contact US: help@patsnap.com