Die-casting die vacuumizing structure with vacuum valve connected with exhaust plates in parallel
A die-casting mold and vacuum valve technology, which is applied in the field of die-casting mold processing, can solve the problems of vacuum valve blockage, slow movement of tributaries, complex shapes, etc.
- Summary
- Abstract
- Description
- Claims
- Application Information
AI Technical Summary
Problems solved by technology
Method used
Image
Examples
Embodiment Construction
[0031] In order to make the object, technical solution and advantages of the present invention clearer, the present invention will be further described in detail below in conjunction with the accompanying drawings and embodiments. It should be understood that the specific embodiments described here are only used to explain the present invention, not to limit the present invention. In addition, the technical features involved in the various embodiments of the present invention described below can be combined with each other as long as they do not constitute a conflict with each other.
[0032] figure 1 It is a schematic layout diagram of a vacuum pumping structure of a die-casting mold in which a vacuum valve and an exhaust plate are connected in parallel according to an embodiment of the present invention. Such as figure 1 As shown, the vacuum structure includes a vacuum valve 2 , an exhaust block 3 and a vacuum control machine 4 . Wherein, one end of the vacuum valve 2 is ...
PUM
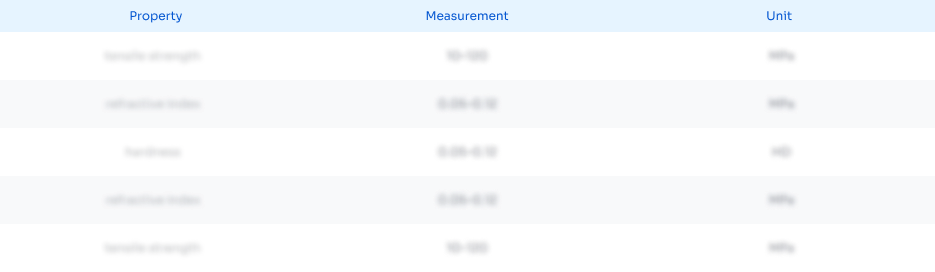
Abstract
Description
Claims
Application Information

- R&D Engineer
- R&D Manager
- IP Professional
- Industry Leading Data Capabilities
- Powerful AI technology
- Patent DNA Extraction
Browse by: Latest US Patents, China's latest patents, Technical Efficacy Thesaurus, Application Domain, Technology Topic, Popular Technical Reports.
© 2024 PatSnap. All rights reserved.Legal|Privacy policy|Modern Slavery Act Transparency Statement|Sitemap|About US| Contact US: help@patsnap.com