Linear piezoelectric motor
A piezoelectric motor and linear technology, applied in electrical components, piezoelectric effect/electrostrictive or magnetostrictive motors, generators/motors, etc., can solve the problem of low output speed, fast wear, complex structure and control circuits and other problems, to achieve the effect of less energy loss, high output speed and simple structure
- Summary
- Abstract
- Description
- Claims
- Application Information
AI Technical Summary
Problems solved by technology
Method used
Image
Examples
Embodiment
[0049] see figure 1 , a linear piezoelectric motor includes a drive preload mechanism, an output mechanism and a bearing seat 2.
[0050] The driving pretension mechanism includes a pair of driving oscillators. A pair of drive vibrator is symmetrically installed on the base 7 through a pair of upright dovetail seats 4, and the position can be adjusted on the base 7. Positioning rod 10 runs through and is connected with a pair of dovetail seat 4; Tightening nut 9, spring 8 is sleeved on the screw rod between dovetail seat 4 and pre-tightening nut 9. A pair of driving vibrator consists of a first driving vibrator 61 and a second driving vibrator 62, see image 3 , the first driving vibrator 61 is provided with a third piezoelectric sheet 63, and the second driving vibrator 62 is provided with a fourth piezoelectric sheet 64;
[0051] see figure 2 , the output mechanism includes an output rod 1, the two ends of the output rod 1 are optical axes, one end of which is connecte...
PUM
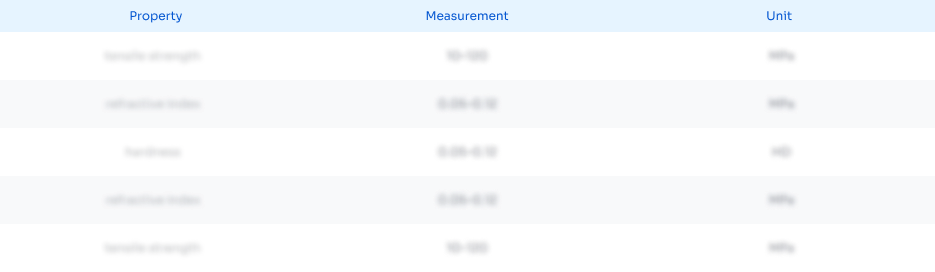
Abstract
Description
Claims
Application Information

- R&D
- Intellectual Property
- Life Sciences
- Materials
- Tech Scout
- Unparalleled Data Quality
- Higher Quality Content
- 60% Fewer Hallucinations
Browse by: Latest US Patents, China's latest patents, Technical Efficacy Thesaurus, Application Domain, Technology Topic, Popular Technical Reports.
© 2025 PatSnap. All rights reserved.Legal|Privacy policy|Modern Slavery Act Transparency Statement|Sitemap|About US| Contact US: help@patsnap.com