Motor zero-position calibration system and method
A technology of zero calibration and calibration method, which is applied in the direction of motor generator testing, electrical measurement, and electrical variable measurement, and can solve problems affecting motor performance, theoretical angle deviation, and influence
- Summary
- Abstract
- Description
- Claims
- Application Information
AI Technical Summary
Problems solved by technology
Method used
Image
Examples
Embodiment Construction
[0025] Such as figure 1 As shown, the motor zero calibration system connects the standard machine 4 with the output shaft of the measured motor 1. The standard machine 4 generally uses a standard motor or dynamometer. The motor position sensor 2 is rigidly connected to the shaft of the measured motor 1. The sensor 2 is used to output the angle signal of the motor rotor. The connection mode and position angle of the measured motor 1 and the position sensor 2 should be consistent with the actual installation. The measured motor 1 and the position sensor 2 can be connected firmly according to the use requirements, as a Perform zero calibration as a whole.
[0026] The output shaft of the standard machine 4 is equipped with a torque sensor 3, the torque measuring instrument is used to measure the actual torque on the motor shaft, the standard machine 4 is used to drive the measured motor 1 to rotate at a constant speed, and the signal processing module 6 is used to receive the motor p...
PUM
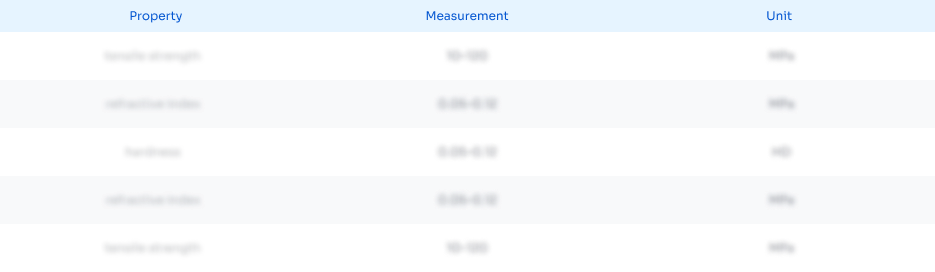
Abstract
Description
Claims
Application Information

- Generate Ideas
- Intellectual Property
- Life Sciences
- Materials
- Tech Scout
- Unparalleled Data Quality
- Higher Quality Content
- 60% Fewer Hallucinations
Browse by: Latest US Patents, China's latest patents, Technical Efficacy Thesaurus, Application Domain, Technology Topic, Popular Technical Reports.
© 2025 PatSnap. All rights reserved.Legal|Privacy policy|Modern Slavery Act Transparency Statement|Sitemap|About US| Contact US: help@patsnap.com