Waste plastic pelleting unit
A technology of waste plastics and granulation, applied in the direction of coating, etc., can solve the problems of uncontrollable feeding amount and uneven feeding speed, etc., and achieve the effect of ensuring health, small installation space and saving space resources
- Summary
- Abstract
- Description
- Claims
- Application Information
AI Technical Summary
Problems solved by technology
Method used
Image
Examples
Embodiment 1
[0048] Such as Figure 1 to Figure 6 As shown, this embodiment provides a waste plastic granulation unit, which includes a storage box 1, a conveying auger 2, a feeding device 3, a screw extruder 4, a cooling device 5, a granulator 6 and a connecting device connected in sequence. The feeding device 7, the feeding device 3 includes a first feed hopper 3-1 and a second feed hopper 3-3, and an intercepting assembly 3-2 is arranged below the first feeding hopper 3-1, and the intercepting assembly 3-2 Including the intercepting plate 3-2.1 and the connecting plate 3-2.2 hollowed out in the middle, the connecting plate 3-2.2 is provided with a groove 3-2.2 / 2 for the sliding of the intercepting plate 3-2.1, hollowed out in the middle of the connecting plate 3-2.2 A feed filter screen 3-2.2 / 1 is detachably arranged at the center, and the lower part of the intercepting assembly 3-2 is connected with the second feed hopper 3-3, and the second feed hopper 3-3 is provided with a residual ...
Embodiment 2
[0057] Such as Figure 7 to Figure 10 As shown, the present embodiment is further optimized on the basis of embodiment 1, specifically:
[0058] The intercepting assembly 3-2 is provided with an electromagnetic vibrator 3-4 that drives the feed filter screen 3-2.2 / 1 to vibrate, and the connection between the first feed hopper 3-1 and the intercepting assembly 3-2 is provided with a first rubber A shock absorbing layer 3-2.3, a second rubber shock absorbing layer 3-2.4 is provided at the connection between the intercepting assembly 3-2 and the second feed hopper 3-3;
[0059] An activated carbon adsorption layer 4-6.1 is arranged in the ultraviolet lamp box 4-6, and the activated carbon adsorption layer 4-6.1 is arranged at intervals with the ultraviolet lamp;
[0060] The cleaning assembly A4-7.6 and the cleaning assembly B for cleaning the filter screen A4-7.4 and the filter screen B4-7.5 are arranged symmetrically on the double slide rail installation frame 4-7.3, and the c...
PUM
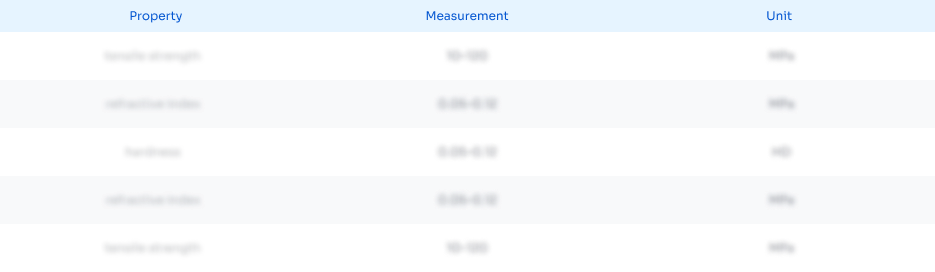
Abstract
Description
Claims
Application Information

- R&D
- Intellectual Property
- Life Sciences
- Materials
- Tech Scout
- Unparalleled Data Quality
- Higher Quality Content
- 60% Fewer Hallucinations
Browse by: Latest US Patents, China's latest patents, Technical Efficacy Thesaurus, Application Domain, Technology Topic, Popular Technical Reports.
© 2025 PatSnap. All rights reserved.Legal|Privacy policy|Modern Slavery Act Transparency Statement|Sitemap|About US| Contact US: help@patsnap.com