Tung oil modified triethylamine cold-box resin component I and production method thereof
A technology of triethylamine and cold core box, applied in the direction of core, casting molding equipment, casting mold, etc., can solve the problems of sand inclusion, cold core box resin sand casting veining, environmental pollution, etc., to improve room temperature performance and High temperature performance, improved humidity resistance and environmental protection performance, the effect of prolonging the usable time
- Summary
- Abstract
- Description
- Claims
- Application Information
AI Technical Summary
Problems solved by technology
Method used
Examples
Embodiment 1
[0040] (1) Melt 25% phenol into the reaction kettle, start the mixer, add tung oil 7%, 10% hydrochloric acid aqueous solution 0.01%, open the steam valve, heat up to 120°C for 40-50min, and keep warm for 1h;
[0041] (2) Cool down to 60°C, add 11% paraformaldehyde, 2% methanol, and 0.04% zinc acetate;
[0042] (3) Heat up to 110±1°C within 40-50min, and react at constant temperature for 1h;
[0043] (4) Heat up to 115±1°C within 15-20min, and react at constant temperature for 1h;
[0044] (5) After the heat preservation is over, continue to heat up and dehydrate under normal pressure. When the temperature in the kettle rises to 120±1°C, time the constant temperature reaction for 0.5h;
[0045] (6) After the constant temperature reaction is over, turn on the vacuum and dehydrate at a vacuum degree of -0.06MPa for 2 hours;
[0046] (7) After dehydration, add 21.95% dibasic acid ester, 25% S-150, 3% cresyl diphenyl phosphate, 4.5% ethyl silicate, stir and cool down;
[0047](8...
Embodiment 2
[0049] (1) Melt 31% phenol into the reaction kettle, start the mixer, add tung oil 2%, 10% hydrochloric acid aqueous solution 0.02%, open the steam valve, heat up to 110°C for 40-50min, and keep warm for 2h;
[0050] (2) Cool down to 60°C, add 15% paraformaldehyde, 1.5% methanol, and 0.06% zinc acetate;
[0051] (3) Heat up to 110±1°C within 40-50min, and react at constant temperature for 0.5h;
[0052] (4) Heat up to 115±1°C within 15-20min, and react at constant temperature for 1h;
[0053] (5) After the heat preservation is over, continue to heat up and dehydrate under normal pressure. When the temperature in the kettle rises to 120±1°C, time and constant temperature reaction for 1.5h;
[0054] (6) After the constant temperature reaction is over, turn on the vacuum and dehydrate at a vacuum degree of -0.07MPa for 1.5h;
[0055] (7) After dehydration, add 24% of dibasic acid ester, 16.92% of S-200, 2.5% of diphenyl-isooctyl phosphate, 6% of ethyl silicate, stir and cool do...
Embodiment 3
[0058] (1) Melt 34% phenol into the reaction kettle, start the mixer, add tung oil 8%, 10% hydrochloric acid aqueous solution 0.03%, open the steam valve, heat up to 100°C for 40-50min, and keep warm for 3h;
[0059] (2) Cool down to 60°C, add 19% paraformaldehyde, 1.5% methanol, and 0.08% zinc acetate;
[0060] (3) Heat up to 110±1°C within 40-50min, and react at constant temperature for 1h;
[0061] (4) Heat up to 115±1°C within 15-20min, and react at constant temperature for 1.5h;
[0062] (5) After the heat preservation is over, continue to heat up and dehydrate under normal pressure. When the temperature in the kettle rises to 120±1°C, time the constant temperature reaction for 1 hour;
[0063] (6) After the constant temperature reaction is over, turn on the vacuum and dehydrate at a vacuum degree of -0.08MPa for 1.5h;
[0064] (7) After dehydration, add 16.89% dibasic acid ester, 14% S-150, 2.5% methyl o-toluate, 3.5% ethyl silicate, stir and cool down;
[0065] (8) W...
PUM
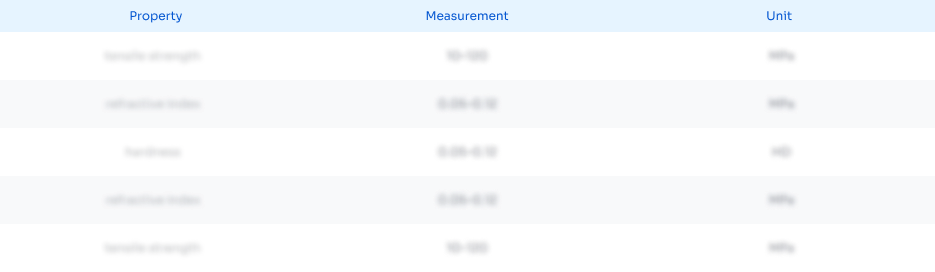
Abstract
Description
Claims
Application Information

- R&D
- Intellectual Property
- Life Sciences
- Materials
- Tech Scout
- Unparalleled Data Quality
- Higher Quality Content
- 60% Fewer Hallucinations
Browse by: Latest US Patents, China's latest patents, Technical Efficacy Thesaurus, Application Domain, Technology Topic, Popular Technical Reports.
© 2025 PatSnap. All rights reserved.Legal|Privacy policy|Modern Slavery Act Transparency Statement|Sitemap|About US| Contact US: help@patsnap.com