Self-test method for railway braking system
A braking system, functional technology, applied in the field of freight train braking system, to achieve the effect of reducing time and reducing train ready time
- Summary
- Abstract
- Description
- Claims
- Application Information
AI Technical Summary
Problems solved by technology
Method used
Image
Examples
Embodiment Construction
[0017] A railroad brake system for freight trains includes a main brake pipe in fluid communication with a brake distributor that is fluidly connected via conduits to relay valves that are each connected to The corresponding relief valves, which are connected to the respective brake cylinders. The brake distributor will typically have integral relay valve capability. Usually there is one relay and one relief valve per bogie, or one relief valve per axle. It is also known to use variable load valves instead of relay valves.
[0018] An auxiliary reservoir is provided which is in fluid communication with the brake distributor via the first outlet and in fluid communication with the respective relay valves via the second outlet. Auxiliary reservoir pressure is protected by a check valve in the distributor. In use, the auxiliary reservoir stores energy in the form of compressed air for applying the brakes. Use the air supply in the brake line to fill the auxiliary reservoir. ...
PUM
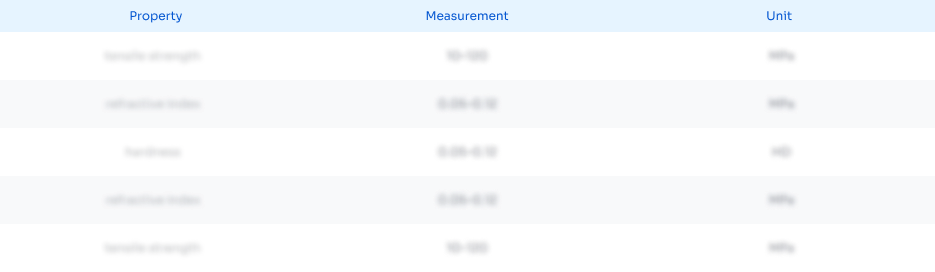
Abstract
Description
Claims
Application Information

- Generate Ideas
- Intellectual Property
- Life Sciences
- Materials
- Tech Scout
- Unparalleled Data Quality
- Higher Quality Content
- 60% Fewer Hallucinations
Browse by: Latest US Patents, China's latest patents, Technical Efficacy Thesaurus, Application Domain, Technology Topic, Popular Technical Reports.
© 2025 PatSnap. All rights reserved.Legal|Privacy policy|Modern Slavery Act Transparency Statement|Sitemap|About US| Contact US: help@patsnap.com