Inductive proximity sensor analog inductance output circuit
A proximity sensor and analog inductance technology, applied in the field of inductive proximity sensors, can solve the problems of inability to achieve zero output, narrow linear working range, delay in inductance value change, etc., to achieve high repetitive positioning accuracy, simple circuit implementation, and anti-interference ability. strong effect
- Summary
- Abstract
- Description
- Claims
- Application Information
AI Technical Summary
Problems solved by technology
Method used
Image
Examples
Embodiment Construction
[0011] refer to figure 1 , In the embodiment described below, an inductive proximity sensor simulates an inductive output circuit, including: an inductive coil L1, an inductive coil L2, an inductance switch circuit and an amplifying output circuit. The inductance coil L1 and the inductance coil L2 are connected in series to the normally open contact 5 of the relay K1, and the other end of the inductance coil L2 is electrically connected to the positive output terminal of the analog inductance circuit through the normally closed contact 4 of the relay K1 and the common terminal contact 3 of the relay. terminal L_HI, the other end of the inductance coil L1 is electrically connected to the negative terminal L_LO of the output terminal of the analog inductance circuit, thereby forming an inductance switching gating switch circuit; The inductance coil L1 of mH and the inductance coil L2 of 1mH are gated, and the selection output of the inductance value of 4.8mH or 5.8mH is realized...
PUM
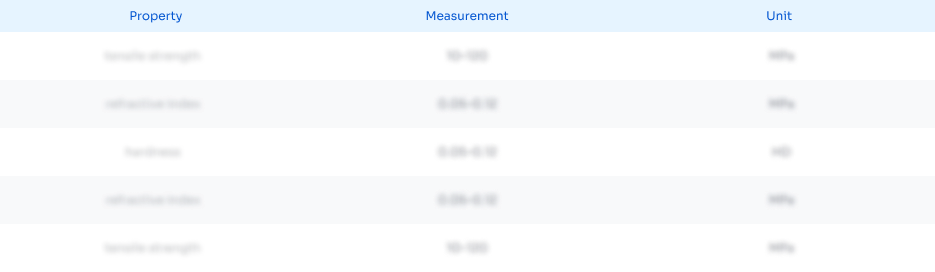
Abstract
Description
Claims
Application Information

- Generate Ideas
- Intellectual Property
- Life Sciences
- Materials
- Tech Scout
- Unparalleled Data Quality
- Higher Quality Content
- 60% Fewer Hallucinations
Browse by: Latest US Patents, China's latest patents, Technical Efficacy Thesaurus, Application Domain, Technology Topic, Popular Technical Reports.
© 2025 PatSnap. All rights reserved.Legal|Privacy policy|Modern Slavery Act Transparency Statement|Sitemap|About US| Contact US: help@patsnap.com