Poly-mercapto compound-containing white carbon black-filled rubber composite material and preparation method thereof
A technology of polymercapto compounds and filling rubber, which is applied in the field of rubber composite materials and its preparation, and can solve problems such as VOC emissions, high energy consumption, and poor dispersion effect of soap-salt dispersants
- Summary
- Abstract
- Description
- Claims
- Application Information
AI Technical Summary
Problems solved by technology
Method used
Image
Examples
Embodiment 1
[0031] Example 1: The formula is: 100 parts by mass of solution-polymerized styrene-butadiene rubber, 100 parts of white carbon black, 10 parts of poly(mercaptylmethyl)siloxane, and other components are: 40 parts of aromatic oil, 5 parts of zinc oxide 2 parts, 2 parts of stearic acid, 2 parts of accelerator CZ, 0.2 parts of accelerator TMTD, 1.5 parts of sulfur, 1.5 parts of antioxidant RD, and 1 part of paraffin. The process is as follows: first mix other raw materials except the accelerator and sulfur in the internal mixer at 60°C for 15 minutes, then add the accelerator and sulfur to the open mill at 20°C after degumming and cooling, and mix well. The vulcanization condition is 160°C, Positive vulcanization time.
Embodiment 2
[0032] Example 2: The formula is: 75 parts by mass of solution-polymerized styrene-butadiene rubber, 25 parts of butadiene rubber, 60 parts of white carbon black, 0.3 part of 1,4 butanedithiol; other components are: 5 parts of zinc oxide, hard 2 parts of fatty acid, 1.8 parts of accelerator CZ, 0.3 parts of accelerator TMTD, 1.5 parts of sulfur, 1.5 parts of anti-aging agent RD, 1 part of paraffin. The process is as follows: first mix other raw materials except the accelerator and sulfur on the open mill at 20°C for 15 minutes, then add the accelerator and sulfur, mix well, and the vulcanization conditions are 160°C and normal vulcanization time.
Embodiment 3
[0033]Example 3: The formula is: 100 parts by mass of natural rubber, 10 parts of white carbon black, 0.01 part of 2,4,6-trimercapto-s-triazine; other components are: 1 part of Si-69 silane coupling agent, carbon 40 parts of black, 5 parts of zinc oxide, 2 parts of stearic acid, 1.8 parts of accelerator NS, 1.5 parts of sulfur, 1.5 parts of anti-aging agent RD, 1 part of paraffin. The process is as follows: first mix other raw materials except the accelerator and sulfur in the internal mixer at 80°C for 10 minutes, then raise the temperature to 200°C and keep the temperature and cut for 0.1 minute, after debinding and cooling, add the accelerator on the mixer at 30°C Mix with sulfur, the vulcanization condition is 150°C and the normal vulcanization time.
PUM
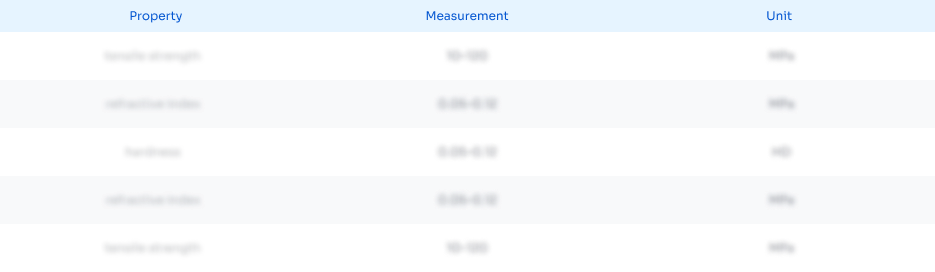
Abstract
Description
Claims
Application Information

- R&D
- Intellectual Property
- Life Sciences
- Materials
- Tech Scout
- Unparalleled Data Quality
- Higher Quality Content
- 60% Fewer Hallucinations
Browse by: Latest US Patents, China's latest patents, Technical Efficacy Thesaurus, Application Domain, Technology Topic, Popular Technical Reports.
© 2025 PatSnap. All rights reserved.Legal|Privacy policy|Modern Slavery Act Transparency Statement|Sitemap|About US| Contact US: help@patsnap.com