Resistance spot welding method
A technology of resistance spot welding and energization, applied in resistance welding equipment, welding equipment, welding power sources, etc., can solve the problems of inability to obtain nuggets, prone to splashing, and narrow range.
- Summary
- Abstract
- Description
- Claims
- Application Information
AI Technical Summary
Problems solved by technology
Method used
Image
Examples
Embodiment
[0110] About Table 1 and Figure 1~4 The group of three overlapping steel plates shown was resistance spot welded under the conditions shown in Table 2 to produce joints.
[0111] Here, the case where the control mode in Table 2 is "constant current" shows the results when welding was performed by constant current control under the welding conditions shown in the table. On the other hand, when the control mode is "adaptive control", test welding is performed under the welding conditions shown in the table without interference such as a plate gap, and the time change of the instantaneous heating value per unit volume is stored. Thereafter, the results of adaptive control welding following the current value were performed based on the time-varying curve of the instantaneous calorific value per unit volume obtained by the test welding.
[0112] In addition, when making a part of the joint, such as Figure 4 As shown, spacers 15 (distance between spacers: 60 mm) were inserted be...
PUM
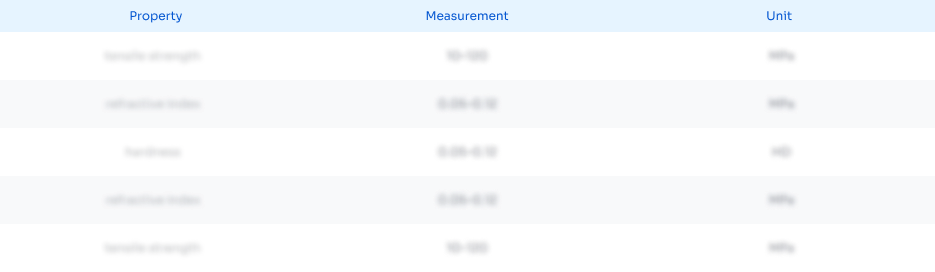
Abstract
Description
Claims
Application Information

- R&D Engineer
- R&D Manager
- IP Professional
- Industry Leading Data Capabilities
- Powerful AI technology
- Patent DNA Extraction
Browse by: Latest US Patents, China's latest patents, Technical Efficacy Thesaurus, Application Domain, Technology Topic, Popular Technical Reports.
© 2024 PatSnap. All rights reserved.Legal|Privacy policy|Modern Slavery Act Transparency Statement|Sitemap|About US| Contact US: help@patsnap.com