Carrying and conveying robot
A technology of robots and actuators, which is applied in the field of robots, can solve the problems of large position deviation of robots and cannot be corrected quickly, and achieve the effects of ensuring stability, avoiding damage to express shipments, and correcting deviations
- Summary
- Abstract
- Description
- Claims
- Application Information
AI Technical Summary
Problems solved by technology
Method used
Image
Examples
Embodiment 1
[0043] The invention relates to a handling and delivery robot. In order to give people a sense of intimacy and design, the present invention designs the overall robot into a very cute shape, and at the same time hides the internal mechanism, which also plays a protective role.
[0044] like figure 1 As shown, the transportation robot includes a visual image acquisition module 80 , an analysis module 90 , a control module 70 , a drive unit 20 and a first execution unit 10 . The analysis module 90 determines the morphological parameters of the goods based on the image information collected by the visual image collection module 80, and automatically identifies the handling mode according to the morphological parameters of the goods. The control module 70 sends control parameters for moving and / or gripping the goods according to the location characteristics of the goods to the drive unit 20 and / or the second execution unit 10 based on the shape parameters of the goods and the ide...
Embodiment 2
[0066]This embodiment is a further improvement on Embodiment 1, and content that is repeated with Embodiment 1 will not be repeated here.
[0067] This embodiment provides a transporting and transporting robot, including a carrying platform provided with a driving device, an actuator, and a control module. The driving device adjusts the speed and direction of the carrying platform based on the control information of the control module to cooperate with the actuator based on the control information of the control module. Moving goods. The transportation of the robot at the specified location from the cargo location requires location guidance, and the transportation and delivery robot also includes a guidance unit that guides the specified location in a wired or wireless manner.
[0068] Preferably, the robot further includes a tape guide unit and a vision guide unit.
PUM
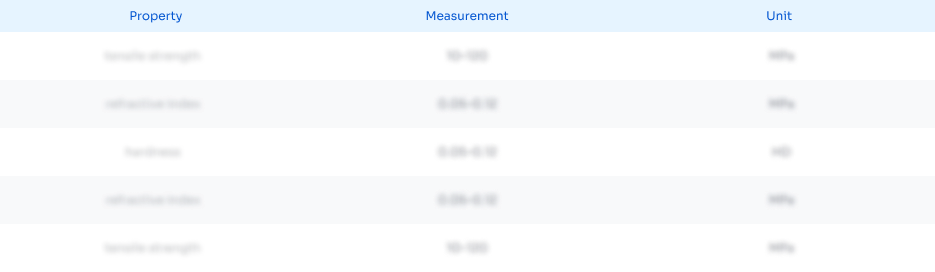
Abstract
Description
Claims
Application Information

- R&D
- Intellectual Property
- Life Sciences
- Materials
- Tech Scout
- Unparalleled Data Quality
- Higher Quality Content
- 60% Fewer Hallucinations
Browse by: Latest US Patents, China's latest patents, Technical Efficacy Thesaurus, Application Domain, Technology Topic, Popular Technical Reports.
© 2025 PatSnap. All rights reserved.Legal|Privacy policy|Modern Slavery Act Transparency Statement|Sitemap|About US| Contact US: help@patsnap.com