A six-dimensional force sensor
A six-dimensional force sensor and sensor technology, applied in instruments, measuring fluid pressure, measuring force components, etc., can solve the problems of high precision requirements of parts, small load bearing in z direction, high degree of coupling of force components, etc., and achieve low precision requirements , low processing cost, and low degree of coupling between dimensions
- Summary
- Abstract
- Description
- Claims
- Application Information
AI Technical Summary
Problems solved by technology
Method used
Image
Examples
Embodiment Construction
[0030] The technical solution of the present invention will be further described in detail below in conjunction with the embodiments and the accompanying drawings.
[0031] Such as figure 1 with figure 2 As shown, a six-dimensional force sensor with overload protection of the present invention includes an upper end cover 1, a housing 2, a sensor base 3, a rubber sealing ring 4, an overload protection mounting plate 5, a bearing end cover 6, and a bearing block 7 , an elastic body 8, a bearing 9, a strain gauge 10, and an acquisition circuit board 11. Among them, the elastic body 8 is used to measure the three component forces F in the space coordinate system x , F y , F z and three moments M x ,M y ,M z . The upper end cover 1 and the sensor base 3 are parallel to each other and fixedly connected to two ends of the shell 2 respectively. The bearing end cover 6 and the bearing block 7 are fixedly connected to the sensor base 3 by bolts respectively, and the bearing 9 ...
PUM
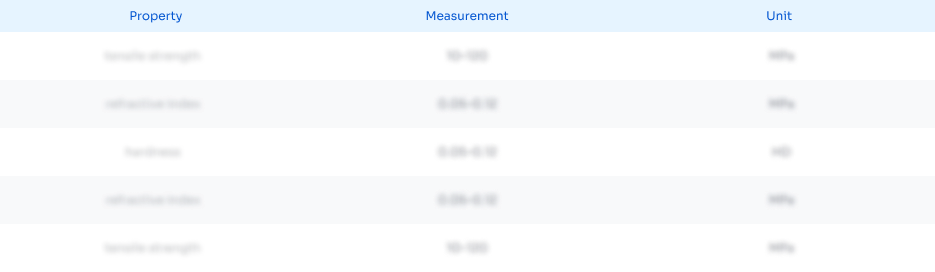
Abstract
Description
Claims
Application Information

- R&D
- Intellectual Property
- Life Sciences
- Materials
- Tech Scout
- Unparalleled Data Quality
- Higher Quality Content
- 60% Fewer Hallucinations
Browse by: Latest US Patents, China's latest patents, Technical Efficacy Thesaurus, Application Domain, Technology Topic, Popular Technical Reports.
© 2025 PatSnap. All rights reserved.Legal|Privacy policy|Modern Slavery Act Transparency Statement|Sitemap|About US| Contact US: help@patsnap.com