Strip vacuum plasma film-plating system
A plasma and coating system technology, applied in the field of plasma coating system, can solve the problems of low coating speed, large force, uneven color, etc., to achieve uniform and single film layer, ensure vacuum degree, and ensure high quality Effect
- Summary
- Abstract
- Description
- Claims
- Application Information
AI Technical Summary
Problems solved by technology
Method used
Image
Examples
Embodiment 1
[0035] Such as Figure 1 to Figure 4 As shown, a strip vacuum plasma coating system includes a vacuum obtaining system 3, a vacuum connecting pipeline 2 and a continuous coating chamber 1 with a circular structure or an elliptical structure, and the vacuum obtaining system 3 connects the continuous vacuum through the vacuum connecting pipeline 2. The coating chamber 1 is connected, and the vacuum obtaining system 3 is a conventional vacuuming device; the continuous coating chamber 1 includes an unwinding device 11, a winding device 12, a heat pipe mechanism 13, an inlet and outlet gas mixing device 14 and a cathode target 15. The filtered cathode target generating device 16, the unwinding device 11, the winding device 12 and the heat pipe mechanism 13 are located inside the continuous coating chamber 1, and the inlet and outlet gas mixing device 14 and the filtered cathode target generating device 15 are located on the side of the continuous coating chamber 1 On the wall, the ...
Embodiment 2
[0047] Such as Figure 3 to Figure 5 As shown, as in the structure of Embodiment 1, a vacuum obtaining system 3 is connected to two continuous vacuum coating chambers 1 through a vacuum connecting pipe 2 . The parts on the vacuum connection pipe 2 that are diverted to the continuous vacuum coating chamber 1 are divided into A and B, and the continuous vacuum coating chamber 1 is divided into a vacuum coating chamber 1 and a vacuum coating chamber 2.
[0048] After the coating in vacuum coating chamber 1 is completed, close the vacuum chamber furnace door of vacuum coating chamber 2, close the first valve, and open the second valve B to allow the gas in vacuum coating chamber 2 to flow into vacuum coating chamber 1. When the vacuum degree reaches equilibrium Finally, after closing the second valve A, open the first valve, vacuumize the vacuum coating chamber two, open the vacuum chamber furnace door 19 of the vacuum coating chamber one simultaneously, load and unload the strip,...
PUM
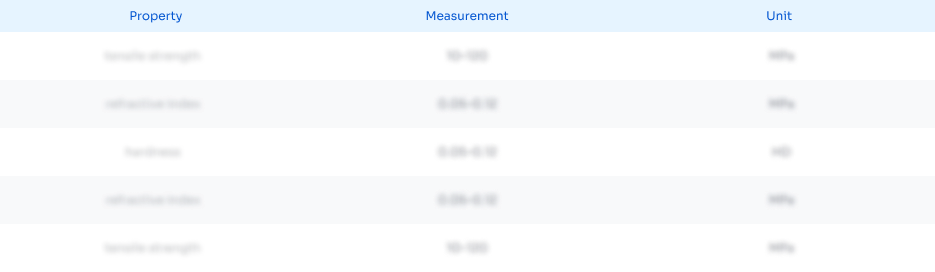
Abstract
Description
Claims
Application Information

- R&D
- Intellectual Property
- Life Sciences
- Materials
- Tech Scout
- Unparalleled Data Quality
- Higher Quality Content
- 60% Fewer Hallucinations
Browse by: Latest US Patents, China's latest patents, Technical Efficacy Thesaurus, Application Domain, Technology Topic, Popular Technical Reports.
© 2025 PatSnap. All rights reserved.Legal|Privacy policy|Modern Slavery Act Transparency Statement|Sitemap|About US| Contact US: help@patsnap.com