Attapulgite mildew-resistant plasterboard and preparation method thereof
A technology for mildew-proof gypsum board and attapulgite clay, which is applied in construction, building structure, covering/lining, etc., can solve the problems of easy mold, easy damage and aging, weak wear resistance of gypsum board, etc., and achieves hard texture. , Improve the effect of sterilization and mildew prevention, good application prospects
- Summary
- Abstract
- Description
- Claims
- Application Information
AI Technical Summary
Problems solved by technology
Method used
Examples
Embodiment 1
[0026] The attapulgite mildew-resistant gypsum board of the present embodiment includes the following raw materials in parts by weight:
[0027] 30 parts of acidified paste attapulgite clay, 5 parts of methylisothiazolinone, 5 parts of dodecyl dimethyl benzyl ammonium chloride, 0.5 part of methyl paraben, 0.5 part of propyl paraben 40 parts, 40 parts of pearl sand, 250 parts of natural dihydrate gypsum, 20 parts of epoxy resin pouring glue, 10 parts of wood fiber, 60 parts of deionized water.
[0028] The preparation method of the attapulgite mildew-proof gypsum board of the present embodiment comprises the following steps:
[0029] Step 1: Mix natural dihydrate gypsum and pearl sand for calcination. The calcination temperature is 800°C and the time is 2 hours. Add the calcined mixture and wood fiber into the mixer and stir evenly. The stirring speed is 900 r / min, and the stirring time is 5 hours, mixture A;
[0030] Step 2, add the acidified paste attapulgite clay, methylis...
Embodiment 2
[0035] The attapulgite mildew-resistant gypsum board of the present embodiment includes the following raw materials in parts by weight:
[0036] 60 parts of acidified paste attapulgite clay, 15 parts of methylisothiazolinone, 15 parts of dodecyl dimethyl benzyl ammonium chloride, 5 parts of methylparaben, 5 parts of propylparaben 60 parts, 60 parts of pearl sand, 350 parts of natural dihydrate gypsum, 40 parts of epoxy resin pouring glue, 20 parts of wood fiber, and 80 parts of deionized water.
[0037] The preparation method of the attapulgite mildew-proof gypsum board of the present embodiment comprises the following steps:
[0038] Step 1: Mix natural dihydrate gypsum and pearl sand for calcination. The calcination temperature is 900°C and the time is 3 hours. Add the calcined mixture and wood fiber into the mixer and stir evenly. The stirring speed is 1200 r / min, and the stirring time is 7 hours, mixture A;
[0039] Step 2, add the acidified paste attapulgite clay, methy...
Embodiment 3
[0044] The attapulgite mildew-resistant gypsum board of the present embodiment includes the following raw materials in parts by weight:
[0045] 45 parts of acidified paste attapulgite clay, 10 parts of methylisothiazolinone, 10 parts of dodecyl dimethyl benzyl ammonium chloride, 3 parts of methylparaben, 3 parts of propylparaben 50 parts, 50 parts of pearl sand, 300 parts of natural dihydrate gypsum, 30 parts of epoxy resin pouring glue, 15 parts of wood fiber, 70 parts of deionized water.
[0046] The preparation method of the attapulgite mildew-proof gypsum board of the present embodiment comprises the following steps:
[0047] Step 1: Mix natural dihydrate gypsum and pearl sand for calcination. The calcination temperature is 850°C and the time is 2.5 hours. Add the calcined mixture and wood fiber into a mixer and stir evenly. The stirring speed is 1000 r / min, and the stirring time is 6 hours, mixture A;
[0048] Step 2, add the acidified paste attapulgite clay, methyliso...
PUM
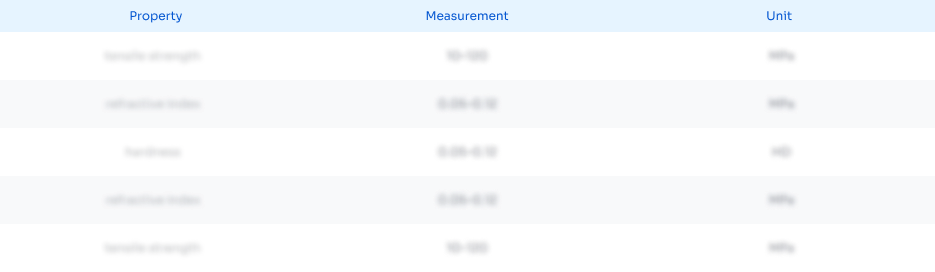
Abstract
Description
Claims
Application Information

- R&D
- Intellectual Property
- Life Sciences
- Materials
- Tech Scout
- Unparalleled Data Quality
- Higher Quality Content
- 60% Fewer Hallucinations
Browse by: Latest US Patents, China's latest patents, Technical Efficacy Thesaurus, Application Domain, Technology Topic, Popular Technical Reports.
© 2025 PatSnap. All rights reserved.Legal|Privacy policy|Modern Slavery Act Transparency Statement|Sitemap|About US| Contact US: help@patsnap.com