Wastewater-discharge-free continuous dyeing technology of microfiber material
A technology without waste water and microfiber, applied in the field of continuous dyeing process, can solve the problems of difficult implementation and large drainage in synthetic leather factories, and achieve the effects of increasing social and environmental costs, improving production efficiency, and high-efficiency dyeing effect
- Summary
- Abstract
- Description
- Claims
- Application Information
AI Technical Summary
Problems solved by technology
Method used
Image
Examples
Embodiment 1
[0031] Such as figure 1 As shown, the superfiber material to be treated is dyed light-colored, and the pad dyeing process adopted includes:
[0032] S1. padding, using acid dye paste to dye the superfiber material through two dipping and two padding processes (of course, one dipping and one padding or other alternate padding multiple padding processes can be used according to the specific requirements of padding) ; And add acid release agent;
[0033] S2. Microwave reaction, using a microwave radiation device to boil and vaporize the acid dye color paste on the superfiber dye until the liquid-carrying rate is 10-15%;
[0034] Of course, due to differences in regional environmental temperature and humidity, and the needs of individual special processes, the liquid retention rate can also be controlled at 8-30%, and even further adjustments can be made, as long as effective dyeing is maintained and a certain liquid retention rate is maintained.
[0035] S301. Pass the superfib...
Embodiment 2
[0039] Such as figure 2 As shown, the superfiber material to be treated is dyed dark, and the pad dyeing process is adopted, and the steps include:
[0040] S1. padding, using acid dye paste to dye the superfiber material through two dipping and two padding processes (of course, one dipping and one padding or other alternate padding multiple padding processes can be used according to the specific requirements of padding) ; And add acid release agent;
[0041] S2. Microwave reaction, using a microwave radiation device to boil and vaporize the acid dye color paste on the superfiber dye until the liquid-carrying rate is 10-15%;
[0042] Of course, due to differences in regional environmental temperature and humidity, and the needs of individual special processes, the liquid retention rate can also be controlled at 8-30%, and even further adjustments can be made, as long as effective dyeing is maintained and a certain liquid retention rate is maintained.
[0043] S21. Cleaning, p...
PUM
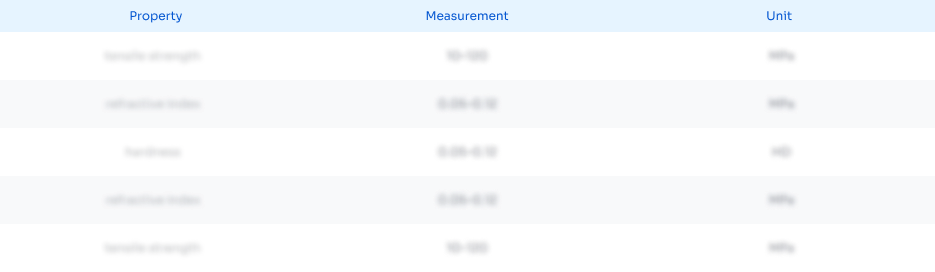
Abstract
Description
Claims
Application Information

- Generate Ideas
- Intellectual Property
- Life Sciences
- Materials
- Tech Scout
- Unparalleled Data Quality
- Higher Quality Content
- 60% Fewer Hallucinations
Browse by: Latest US Patents, China's latest patents, Technical Efficacy Thesaurus, Application Domain, Technology Topic, Popular Technical Reports.
© 2025 PatSnap. All rights reserved.Legal|Privacy policy|Modern Slavery Act Transparency Statement|Sitemap|About US| Contact US: help@patsnap.com