Hollow floor of through beam
A cavity floor and main beam technology, applied to floors, building components, buildings, etc., can solve problems such as construction, weight, and cost
- Summary
- Abstract
- Description
- Claims
- Application Information
AI Technical Summary
Problems solved by technology
Method used
Image
Examples
Embodiment Construction
[0020] The invention will be further described below in conjunction with the accompanying drawings.
[0021] figure 1 It is an elevation view of a perforated steel mesh body of a hollow floor through beam of the present invention. When the present invention is implemented, the ribbed steel mesh 2 prepared from the factory is transported to the construction site; Produce foamed cement blocks of the required specifications nearby or at the construction site; place foamed cement blocks at 4 places on the cut-to-length mold marks of the ribbed steel mesh, and wrap the foamed cement blocks with the ribbed steel mesh along the scaled die marks, The foam cement block is a support foam cement block 34 and a plugging foam cement block 35, a prefabricated notch 36 is arranged at the lower end of the support foam cement block 34, and N reserved holes 37 are arranged in the support foam cement block; There is a prefabricated notch 3 on the inner wall of the cement block; the two ends of ...
PUM
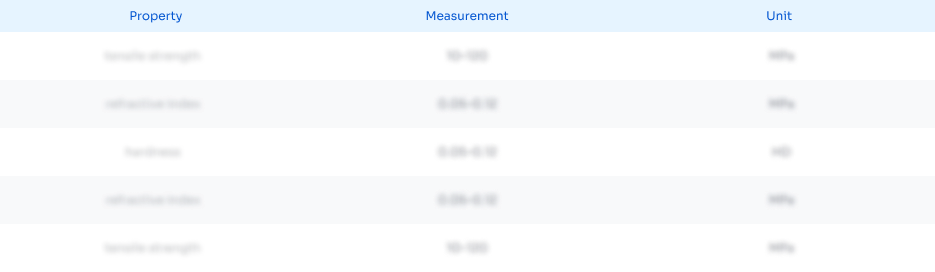
Abstract
Description
Claims
Application Information

- R&D
- Intellectual Property
- Life Sciences
- Materials
- Tech Scout
- Unparalleled Data Quality
- Higher Quality Content
- 60% Fewer Hallucinations
Browse by: Latest US Patents, China's latest patents, Technical Efficacy Thesaurus, Application Domain, Technology Topic, Popular Technical Reports.
© 2025 PatSnap. All rights reserved.Legal|Privacy policy|Modern Slavery Act Transparency Statement|Sitemap|About US| Contact US: help@patsnap.com