Manufacturing method of rolling roller inlaid with hard alloy nails
A technology of hard alloy and manufacturing method, which is applied in the field of casting, and can solve problems such as hard alloy nails falling off, easy cracks, and roll sleeve failure.
- Summary
- Abstract
- Description
- Claims
- Application Information
AI Technical Summary
Problems solved by technology
Method used
Image
Examples
Embodiment Construction
[0017] Below in conjunction with embodiment the present invention is described in further detail:
[0018] The invention relates to a manufacturing method of a cemented carbide nailed roller. The cemented carbide nailed roller is composed of a roller core and a roller cover, wherein the roller cover is produced by a centrifugal casting method, and the alloy is cast by centrifugal and compound casting methods. The nails are directly cast on the outer surface of the roller sleeve, and the centrifugal and composite casting of the roller sleeve needs to be completed with the help of centrifugal tooling, such as figure 1 As shown, the centrifugal tooling includes a cold-type tooling 3, a tooling cold-type 4, a tooling upper end cover 2, a tooling lower end cover 5, and a fastening pin 1, which match the outer diameter and height of the roller sleeve and the inner surface is fixed with an alloy nail. , wherein the tooling cold type 4 is a cylinder with steps at both ends, the cold t...
PUM
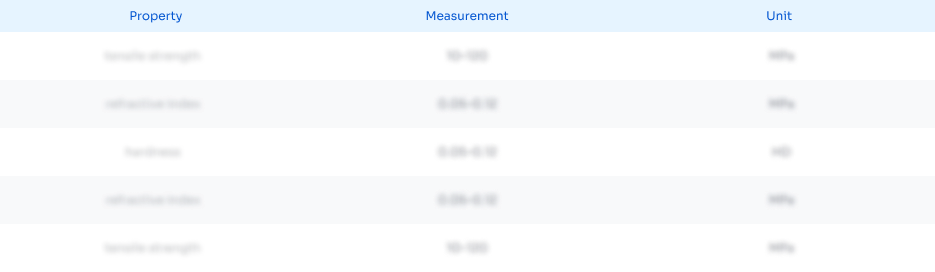
Abstract
Description
Claims
Application Information

- R&D
- Intellectual Property
- Life Sciences
- Materials
- Tech Scout
- Unparalleled Data Quality
- Higher Quality Content
- 60% Fewer Hallucinations
Browse by: Latest US Patents, China's latest patents, Technical Efficacy Thesaurus, Application Domain, Technology Topic, Popular Technical Reports.
© 2025 PatSnap. All rights reserved.Legal|Privacy policy|Modern Slavery Act Transparency Statement|Sitemap|About US| Contact US: help@patsnap.com