Linear axis geometric error detecting method of five-axis numerically-controlled machine tool
A geometric error, CNC machine tool technology, used in measuring/indicating equipment, metal processing mechanical parts, metal processing equipment, etc., can solve the problem of inability to achieve simultaneous detection of multiple errors, limited measurement accuracy Long cycle and other issues
- Summary
- Abstract
- Description
- Claims
- Application Information
AI Technical Summary
Problems solved by technology
Method used
Image
Examples
Embodiment Construction
[0050] The specific embodiments of the present invention will be described in detail below in conjunction with the technical solutions and accompanying drawings.
[0051] The invention adopts three cameras to collect image information of a characteristic target ball fixed on a workbench and moves linearly with the machine tool, and through comprehensive data processing, the geometric error of the linear axis of the machine tool is solved. figure 1 It is a diagram of a geometric error detection device for machine tool linear axes based on trinocular vision. Cameras 1, 2, and 3 are installed on the camera adjustment frame 4 respectively, and the characteristic target balls 5 of B, A, and C , 6, 7 are installed on the machine tool table 8 respectively.
[0052] Adjust the position of each camera so that the optical axis of No. 1 camera 1 is parallel to the X-axis direction of the machine tool; the 2 optical axis of No. 2 camera is parallel to the Y-axis direction of the machine t...
PUM
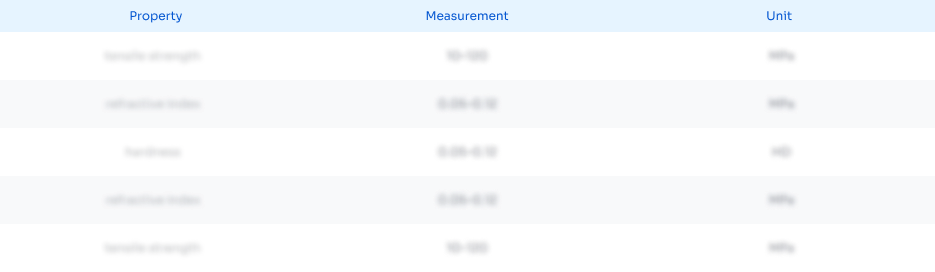
Abstract
Description
Claims
Application Information

- R&D Engineer
- R&D Manager
- IP Professional
- Industry Leading Data Capabilities
- Powerful AI technology
- Patent DNA Extraction
Browse by: Latest US Patents, China's latest patents, Technical Efficacy Thesaurus, Application Domain, Technology Topic, Popular Technical Reports.
© 2024 PatSnap. All rights reserved.Legal|Privacy policy|Modern Slavery Act Transparency Statement|Sitemap|About US| Contact US: help@patsnap.com