Special-shaped section metal hollow component six-axis free bending forming device and technology analysis method
A technology for hollow components and special-shaped cross-sections, which is applied in the field of six-axis free bending forming equipment for hollow components with special-shaped cross-sections, and can solve the problems of flat cross-sections, limited degrees of freedom, and labor and material resources.
- Summary
- Abstract
- Description
- Claims
- Application Information
AI Technical Summary
Problems solved by technology
Method used
Image
Examples
Embodiment 1
[0097] Step 1), reference figure 2 , for the square tube to be bent, feed the material horizontally at a speed of 10mm / s, start the equipment X-axis motor (9), and make the bending die (1) produce an eccentricity of 1mm in the X-axis direction. Continue to feed the material to obtain the bending radius of the square tube when the eccentricity is 1 mm. Repeat the test to obtain the bending radius of the square tube when the eccentricity is 2mm, 3mm, 4mm, 5mm, 6mm..., and then obtain a series of relationship points between the eccentricity and the bending radius for the square tube;
[0098] In step 2), a series of points obtained in step 1) are fitted to obtain a relationship curve between eccentricity and bending radius for the specific square tube.
[0099] Step 3), will be as figure 2 The three-dimensional geometric model of the square pipe shown is segmented, including straight and curved segments;
[0100] Step 4), obtain the first straight section of the square tube ...
Embodiment 2
[0127] Step 1), reference image 3 , for the I-shaped cross-section profile to be bent, feed the material horizontally at a speed of 10mm / s, start the X-axis movement motor of the equipment, and make the bending die produce an eccentricity of 1mm in the X-axis direction. Continue to feed the material to obtain the bending radius of the I-shaped cross-section profile when the eccentricity is 1 mm. Repeat the test to obtain the bending radius of the I-shaped section profile when the eccentricity is 2mm, 3mm, 4mm, 5mm, 6mm..., and then obtain a series of relationship points between the eccentricity and the bending radius for the I-shaped section ;
[0128] In step 2), a series of points obtained in step 1) are fitted to obtain a relationship curve between the eccentricity and the bending radius of the specific I-shaped cross-section profile.
[0129] Step 3), will be as image 3 The three-dimensional geometric model of the shown I-shaped section bar is segmented, including the...
Embodiment 3
[0157] Step 1), for the to be bent such as Figure 4 The special-shaped cross-section pipe shown is fed horizontally at a speed of 10mm / s, and the X-axis movement motor of the equipment is started to make the bending die produce an eccentricity of 1mm in the X-axis direction. Continuously feed the material to obtain the bending radius of the special-shaped cross-section pipe when the eccentricity is 1 mm. Repeat the test to obtain the bending radius of the special-shaped cross-section pipe when the eccentricity is 2mm, 3mm, 4mm..., and then obtain a series of relationship points between the eccentricity and the bending radius for the special-shaped cross-section pipe;
[0158] Step 2): Fitting a series of points obtained in step 1) to obtain a relationship curve between the eccentricity and the bending radius for the pipe with special-shaped cross-section.
[0159] Step 3), will be as Figure 4 The three-dimensional geometric model of the special-shaped cross-section pipe sh...
PUM
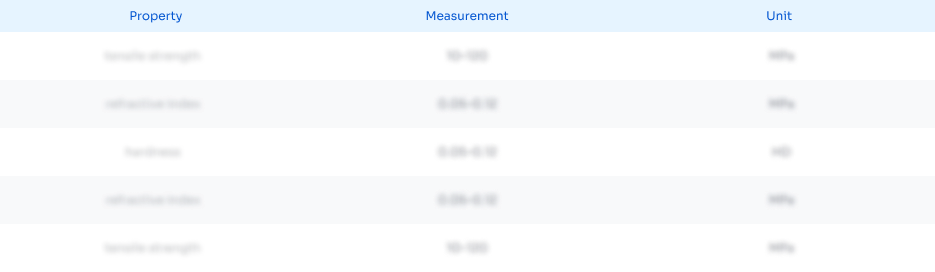
Abstract
Description
Claims
Application Information

- R&D
- Intellectual Property
- Life Sciences
- Materials
- Tech Scout
- Unparalleled Data Quality
- Higher Quality Content
- 60% Fewer Hallucinations
Browse by: Latest US Patents, China's latest patents, Technical Efficacy Thesaurus, Application Domain, Technology Topic, Popular Technical Reports.
© 2025 PatSnap. All rights reserved.Legal|Privacy policy|Modern Slavery Act Transparency Statement|Sitemap|About US| Contact US: help@patsnap.com