Method and device for air-jet assisted center frame damping and adjusting steam turbine air seal
An auxiliary center, steam turbine technology, applied in mechanical equipment, engine components, machines/engines, etc., to achieve the effect of reducing steam leakage, maintaining stability, and reducing radial runout
- Summary
- Abstract
- Description
- Claims
- Application Information
AI Technical Summary
Problems solved by technology
Method used
Image
Examples
specific Embodiment approach 1
[0045] Specific implementation mode one: the following combination Figure 6 to Figure 10 This embodiment will be specifically described. This implementation mode is realized through the following steps:
[0046] 1. Start the steam turbine; before starting, the gap t between the surface of the inner hole of the air seal assembly at the top of the moving blade of the steam turbine and the outer surface of the turbine blade is between 1.5 and 10 mm;
[0047] 2. After the steam turbine reaches the normal speed, adjust the auxiliary support assembly arranged at the inner hole of the diaphragm, so that the upper and lower bearing pads on the auxiliary support assembly gradually close together and surround the main shaft of the steam turbine to reduce the radial runout of the main shaft of the steam turbine ; In the initial state, the distance between the inner surface of the upper bearing bush 7-1 and the lower bearing bush 7-2 on the auxiliary support assembly and the surface of ...
specific Embodiment approach 2
[0057] Specific implementation mode two: the following combination Image 6 and Figure 8 This embodiment will be specifically described. This embodiment is compared with Embodiment 1: this method also includes three groups of distance sensors 6-14 and a group of vibration sensors 8-5, and the first group of distance sensors 6-14 is arranged on the air seal body 6-11 to Real-time measurement of the gap between the gas seal body 6-11 and the outer surface of the steam turbine blade 6-12 and the radial runout of the outer surface of the steam turbine blade 6-12; the second group of distance sensors 8-4 are respectively arranged on the push rod 8-2 At the front end, the distance between the roller 8-1 and the steam turbine main shaft 9-3 and the radial runout of the steam turbine main shaft 9-3 are measured in real time; the third group of distance sensors is arranged on the upper bearing bush 7-1 and the lower bearing bush 7-2 , to measure the gap between the upper bearing bus...
specific Embodiment approach 3
[0061] Specific implementation mode three: the following combination Image 6 This embodiment will be specifically described. The fifth step of this embodiment also includes the following technical means. During the process of making the surface of the inner hole of the air seal assembly at the top of the moving blade close to the outer surface of the steam turbine blade 6-12, the air seal body 6-11 and the steam turbine blade 6 are collected in real time. -12 The gap on the outer surface and the radial runout on the outer surface of the steam turbine blade 6-12 and the vibration data collected by the vibration sensor 8-5, to ensure that the value of the gap t is always greater than the value of the radial runout, if the vibration data increases abnormally , then immediately reverse the action to increase the distance between the surface of the inner hole of the air seal assembly at the top of the rotor blade and the outer surface of the turbine blade, and resume operation whe...
PUM
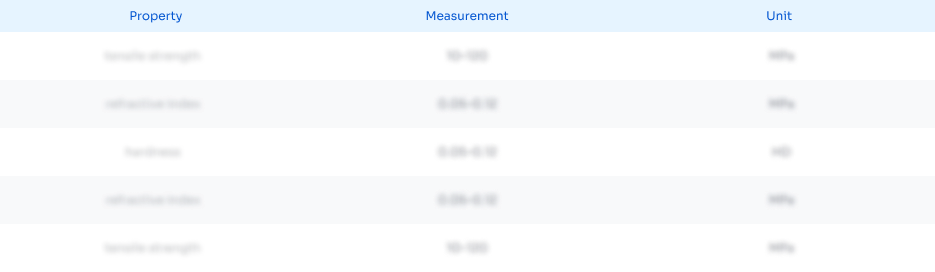
Abstract
Description
Claims
Application Information

- R&D Engineer
- R&D Manager
- IP Professional
- Industry Leading Data Capabilities
- Powerful AI technology
- Patent DNA Extraction
Browse by: Latest US Patents, China's latest patents, Technical Efficacy Thesaurus, Application Domain, Technology Topic, Popular Technical Reports.
© 2024 PatSnap. All rights reserved.Legal|Privacy policy|Modern Slavery Act Transparency Statement|Sitemap|About US| Contact US: help@patsnap.com