Production method of ultra-low silicon peritectic steel
A production method and silicon package technology, applied in the direction of manufacturing converters, etc., can solve problems such as universality to be tested and so on
- Summary
- Abstract
- Description
- Claims
- Application Information
AI Technical Summary
Benefits of technology
Problems solved by technology
Method used
Image
Examples
Embodiment 1
[0043] The production process of ultra-low silicon peritectic steel is: hot metal desulfurization→converter smelting→RH treatment→slab continuous casting.
[0044] Converter 100t in the embodiment, RH refining 100t, slab continuous casting slab width is 800mm, and thickness is 200mm, and concrete operation steps and each procedure process parameter control are as follows:
[0045] 1. Desulfurization of molten iron: After spraying magnesium powder and lime on the ladle for desulfurization, use a slag remover to remove the slag until there is no slag on the surface of the molten iron, and enter the molten iron [S]=0.003%.
[0046] 2. Converter smelting
[0047] 1) The flue gas analysis is combined with the static model for smelting, the blowing process controls the end point temperature to 1710°C, and the end point oxygen level = 450ppm.
[0048] 2) Use the slag blocking method of combining the front slag blocking plate, the rear slag blocking cone and the sliding plate to stri...
Embodiment 2
[0067] The production process of ultra-low silicon peritectic steel is: hot metal desulfurization→converter smelting→RH treatment→slab continuous casting.
[0068] Converter 100t in the embodiment, RH refining 100t, slab continuous casting slab width is 960mm, and thickness is 200mm, and concrete operation steps and each procedure process parameter control are as follows:
[0069] 1. Desulfurization of molten iron: After spraying magnesium powder and lime on the ladle for desulfurization, use a slag scooper to remove the slag until there is no slag on the surface of the molten iron, and enter the molten iron [S]=0.0025%.
[0070] 2. Converter smelting
[0071] 1) The flue gas analysis is combined with the static model for smelting, the blowing process controls the end point temperature to 1725°C, and the end point oxygen level = 700ppm.
[0072] 2) Use the slag blocking method of combining the front sliding plate, the rear slag blocking cone and the sliding plate to strictly ...
Embodiment 3
[0090] The production process of ultra-low silicon peritectic steel is: hot metal desulfurization→converter smelting→RH treatment→slab continuous casting.
[0091] Converter 100t in the embodiment, RH refining 100t, slab continuous casting slab width is 1550mm, and thickness is 200mm, and concrete operation steps and each procedure process parameter control are as follows:
[0092] 1. Desulfurization of hot metal: After spraying magnesium powder and lime on the ladle for desulfurization, use a slag catcher to remove the slag until there is no slag on the surface of the molten iron, and enter the molten iron [S]=0.0016%.
[0093] 2. Converter smelting
[0094] 1) The flue gas analysis is combined with the static model for smelting, the blowing process controls the end point temperature to 1740°C, and the end point oxygen level = 800ppm.
[0095] 2) Use the slag blocking method of combining the front slag blocking plate, the rear slag blocking cone and the sliding plate to stri...
PUM
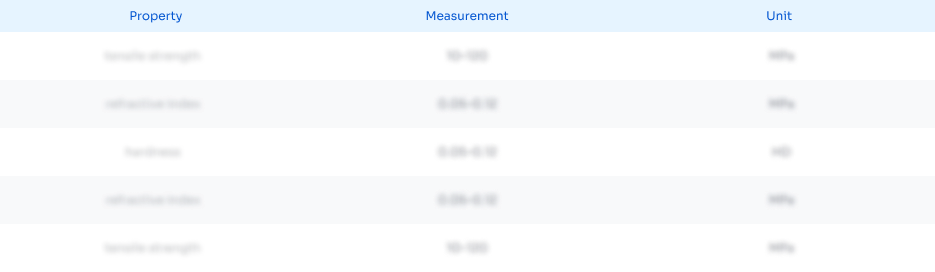
Abstract
Description
Claims
Application Information

- R&D
- Intellectual Property
- Life Sciences
- Materials
- Tech Scout
- Unparalleled Data Quality
- Higher Quality Content
- 60% Fewer Hallucinations
Browse by: Latest US Patents, China's latest patents, Technical Efficacy Thesaurus, Application Domain, Technology Topic, Popular Technical Reports.
© 2025 PatSnap. All rights reserved.Legal|Privacy policy|Modern Slavery Act Transparency Statement|Sitemap|About US| Contact US: help@patsnap.com