Preparation method of matte glaze sanitary ceramic
A technology of sanitary ceramics and matt glaze, which is applied in the field of ceramics, can solve the problems affecting the compactness of glaze, high refractive index, and limited application, and achieve the effect of stable and pure color development, smooth surface, and individuality
- Summary
- Abstract
- Description
- Claims
- Application Information
AI Technical Summary
Problems solved by technology
Method used
Image
Examples
Embodiment 1
[0036]The preparation of the silver-gray matte glaze sanitary ceramics in the present embodiment is realized according to the following steps: One, take by weighing 27.8% quartz, 26.7% Changting potassium feldspar, 13.55% calcite, 3.84% dolomite, 3.1% Zhangzhou Kaolin, 10% zirconium silicate, 9.83% aluminum oxide, 3.2% zinc oxide, appropriate amount of sodium carboxymethylcellulose and soda ash are loaded into a ball mill, and water is added for ball milling. Wherein, the quality of sodium carboxymethyl cellulose and soda ash accounts for 0.03% and 1.95% of the total mass of raw materials respectively. Material: Ball: The ratio of water is 1:1.2:0.45~0.5, and the ball milling is completed when the particle size of the slurry is less than 10 μm and the proportion is greater than 60%, so as to obtain a uniform basic glaze slurry; 2. In the basic glaze slurry prepared in step 1 Add 1% silver-gray material (main components: Sn and Sb), continue ball milling until the particle size...
Embodiment 2
[0038] The difference between this embodiment and Example 1 is that the composition ratios in step one are 27.8% quartz, 26.7% Changting potassium feldspar, 14.55% calcite, 3.83% dolomite, 3% Zhangzhou kaolin, 10% zirconium silicate , 9.83% aluminum oxide, 3.2% zinc oxide. The quality of sodium carboxymethyl cellulose and soda ash accounts for 0.03% and 1.06% of the total mass of raw materials respectively. The firing temperature in step 3 is 1220° C., and the firing time is 15 hours. The CR-10 color difference meter produced by the Japanese KONICA manufacturer was used to measure the L value of the product to be 75.1, a (red value): 0.3, b (yellow value): -0.5. Adopt KGZ-1A gloss meter to measure the glossiness of the product obtained in this embodiment to be 10.6. Other steps and parameters are the same as in Example 1.
Embodiment 3
[0040] The difference between this embodiment and Example 1 is that the composition ratios in step one are 28.2% quartz, 26.8% Changting potassium feldspar, 13.55% calcite, 3.9% dolomite, 3.21% Zhangzhou kaolin, 10% zirconium silicate , 9.93% aluminum oxide, 3.3% zinc oxide. The quality of sodium carboxymethylcellulose and soda ash accounts for 0.03% and 1.14% of the total mass of raw materials respectively. The firing temperature in step 3 is 1240° C., and the firing time is 15.5 hours. The CR-10 color difference meter produced by the Japanese KONICA manufacturer was used to measure the L value of the product to be 78.7, a (red value): 0.5, b (yellow value): -1. Adopt KGZ-1A gloss meter to measure the glossiness of the product obtained in this embodiment to be 14.0. Other steps and parameters are the same as in Example 1.
PUM
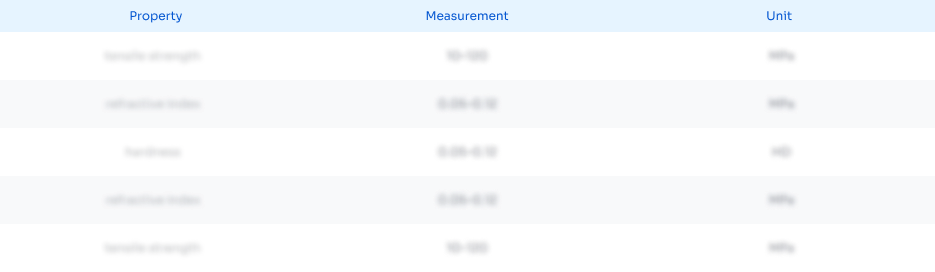
Abstract
Description
Claims
Application Information

- R&D
- Intellectual Property
- Life Sciences
- Materials
- Tech Scout
- Unparalleled Data Quality
- Higher Quality Content
- 60% Fewer Hallucinations
Browse by: Latest US Patents, China's latest patents, Technical Efficacy Thesaurus, Application Domain, Technology Topic, Popular Technical Reports.
© 2025 PatSnap. All rights reserved.Legal|Privacy policy|Modern Slavery Act Transparency Statement|Sitemap|About US| Contact US: help@patsnap.com