Color master batch production technology
A technology of production process and color masterbatch, which is applied in the field of color masterbatch production technology, can solve the problems of inaccurate toner ratio, dust in the working environment, color deviation, etc., and achieve improved accuracy, good color stability and small color deviation Effect
- Summary
- Abstract
- Description
- Claims
- Application Information
AI Technical Summary
Problems solved by technology
Method used
Image
Examples
Embodiment 1
[0022] Embodiment one, prepare red color masterbatch:
[0023] The purchased red toner is melted and extruded by a twin-screw extruder, then cooled by cooling water, and pelletized to make base color particles. The selected red toner is an inorganic toner; it is configured according to the ratio of the color masterbatch formula, and the color masterbatch includes a colorant, a carrier and a dispersant. In this embodiment, the colorant is a red primary color particle, the carrier is a PP chip, and the dispersant It is polyethylene low-molecular wax, the mass percentage of red base color particles is 40%, the mass percentage of carrier PP chips is 59.5%, and the mass percentage of dispersant is 0.5%. According to the quantity required by the customer, weigh each component according to the weight, and stir evenly to obtain the mixed material.
[0024] The materials obtained above are fed into the extruder, and after crushing, shearing and mixing, heating and melting, and extrusi...
Embodiment 2
[0025] Embodiment two, prepare blue masterbatch:
[0026] The difference with the embodiment is that the blue toner is made into blue primary color particles, the selected blue toner is inorganic toner, the carrier used is PET chips, and the dispersant is stearate. According to customer requirements, the function Sexual additive antimicrobial agent. The type of functional additives to be added depends on the requirements of the customer. The mass percentage of the blue base color particles is 30%, the mass percentage of the carrier PET chip is 69%, the mass percentage of the dispersant is 0.5%, and the mass percentage of the antibacterial agent is 0.5%. The preparation steps of the blue color masterbatch are consistent with the steps of the red color masterbatch in Example 1. The melt temperature required in the extruder is compatible with the physical properties of the PET chips and blue base color particles used.
Embodiment 3
[0027] Embodiment three, prepare blue masterbatch:
[0028] The difference from Example 2 is that no functional additives are added according to the requirements of the customer, and the selected blue toner is an inorganic toner; the carrier used is PA slices, and the dispersant is white oil. The mass percentage of the blue primary color particles is 40%, the mass percentage of the carrier PA chip is 59%, and the mass percentage of the dispersant is 1%. The melting temperature required in the extruder should be adapted to the physical properties of the PA chip and blue base color particles used.
PUM
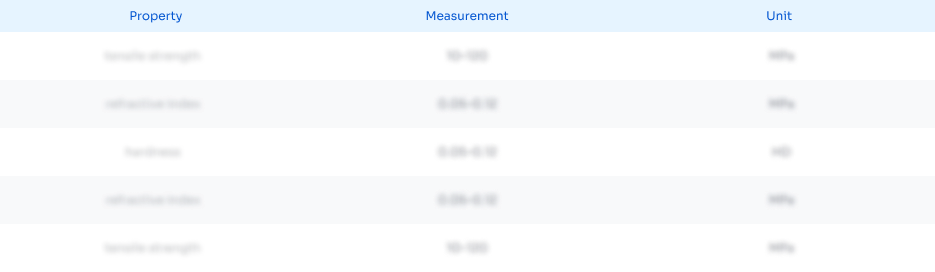
Abstract
Description
Claims
Application Information

- R&D
- Intellectual Property
- Life Sciences
- Materials
- Tech Scout
- Unparalleled Data Quality
- Higher Quality Content
- 60% Fewer Hallucinations
Browse by: Latest US Patents, China's latest patents, Technical Efficacy Thesaurus, Application Domain, Technology Topic, Popular Technical Reports.
© 2025 PatSnap. All rights reserved.Legal|Privacy policy|Modern Slavery Act Transparency Statement|Sitemap|About US| Contact US: help@patsnap.com