Air-floating-type flexible pulling butt joint assembling platform
An assembly platform, air-floating technology, used in metal processing, metal processing equipment, manufacturing tools, etc., can solve the problems of poor flexibility, poor docking compliance, and complex mechanism, so as to improve flexibility adaptability and improve docking compliance. degree, the effect of simplifying the degree of complexity
- Summary
- Abstract
- Description
- Claims
- Application Information
AI Technical Summary
Problems solved by technology
Method used
Image
Examples
specific Embodiment approach 1
[0015] Specific implementation mode one: combine Figure 1 to Figure 5 Describe this embodiment, an air-floating flexible traction and docking assembly platform described in this embodiment includes a front docking traction bracket 3, a rear docking traction bracket 5, a flexible traction mechanism 4 and an air flotation platform 6, and the front docking traction bracket 3 It is arranged at the lower end of the first docking assembly 1, the rear docking traction bracket 5 is arranged at the lower end of the second docking assembly 2, and the front docking traction bracket 3 and the rear docking traction bracket 5 are arranged on the air bearing platform 6 along the length direction. On the end face, one end of the flexible traction mechanism 4 is arranged on the upper end surface of the air bearing platform 6, the other end of the flexible traction mechanism 4 is arranged on the rear docking traction bracket 5, and the front docking traction bracket 3 realizes the first docking...
specific Embodiment approach 2
[0019] Specific implementation mode two: combination Figure 1 to Figure 3 Describe this embodiment, the front docking traction bracket 3 described in this embodiment includes a front lifting platform 3-3, a pitching platform 3-6, a support mechanism 3-7, a front floating platform 3-9, a front motor 3-11, a front Slide block 3-12, two front brackets 3-1, two front elevators 3-4 and four front air feet 3-10, four corners of the front floating platform 3-9 lower end face are respectively provided with a front Air feet 3-10, two front elevators 3-4 are arranged on one side of the upper end surface length direction of the front floating platform 3-9, and the two front elevators 3-4 are arranged along the width direction of the front floating platform 3-9. Lift 3-4 is connected with front motor 3-11, and the upper end of two front lifts 3-4 is fixedly connected with front lifting platform 3-3, and the upper end face of front lifting platform 3-3 is along the width direction of floa...
specific Embodiment approach 3
[0030] Specific implementation mode three: combination Figure 1 to Figure 3 To illustrate this embodiment, the front docking traction bracket 3 in this embodiment further includes a front reducer 3-5, and the front motor 3-11 is connected to the front elevator 3-4 through the front reducer 3-5. Other compositions and connection methods are the same as those in the second embodiment.
PUM
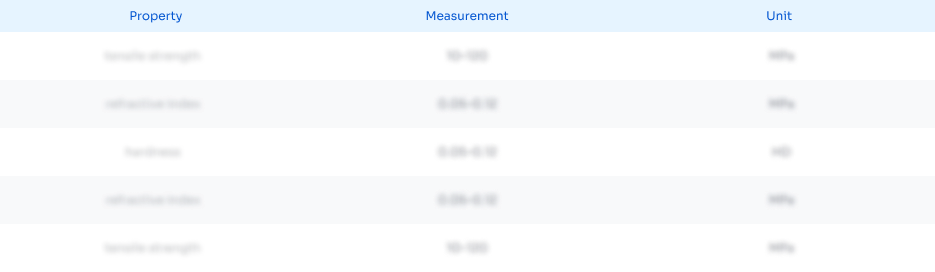
Abstract
Description
Claims
Application Information

- Generate Ideas
- Intellectual Property
- Life Sciences
- Materials
- Tech Scout
- Unparalleled Data Quality
- Higher Quality Content
- 60% Fewer Hallucinations
Browse by: Latest US Patents, China's latest patents, Technical Efficacy Thesaurus, Application Domain, Technology Topic, Popular Technical Reports.
© 2025 PatSnap. All rights reserved.Legal|Privacy policy|Modern Slavery Act Transparency Statement|Sitemap|About US| Contact US: help@patsnap.com