Automobile front ventilation partition material and preparation method thereof
A technology for ventilation clapboards and automobiles, which is applied to the material of automobile front ventilation clapboards and the field of preparation thereof, can solve the problems of low tensile strength, poor aging resistance of materials, poor flame retardant performance, etc., and achieves tensile strength. High strength, high molding efficiency, good flame retardant performance
- Summary
- Abstract
- Description
- Claims
- Application Information
AI Technical Summary
Problems solved by technology
Method used
Image
Examples
Embodiment 1
[0017] A material for the front ventilating partition of an automobile, made of the following materials in parts by weight, including 45 parts of polypropylene, 8 parts of carbon fiber, 9 parts of polyetherimide, 10 parts of polyarylate, and polyvinylidene fluoride 22 parts, 8 parts of alkyd resin, 5 parts of dimethyl silicone oil, 13 parts of nano magnesium oxide, 18 parts of sodium lauryl sulfate, 10 parts of fatty acid polyethylene glycol ester, 16 parts of boric acid alkyl alcohol amide, trichloro 7 parts of fluoromethane, 10 parts of magnesite gel, 6 parts of butylated hydroxyanisole, 5 parts of antimony trioxide, 6 parts of dibutyl phthalate, 8 parts of lauric acid monoglyceride and 13 parts of butyl acrylate .
[0018] A method for preparing the material of the front ventilating partition of an automobile includes the following steps:
[0019] 1) Combine 45 parts of polypropylene, 8 parts of carbon fiber, 9 parts of polyetherimide, 10 parts of polyarylate, 22 parts of polyv...
Embodiment 2
[0024] A material for the front ventilating partition of an automobile, which is made of the following materials in parts by weight, including 50 parts of polypropylene, 11 parts of carbon fiber, 12 parts of polyetherimide, 11 parts of polyarylate, and polyvinylidene fluoride 23.5 parts, 9 parts of alkyd resin, 6.5 parts of dimethyl silicone oil, 14 parts of nano-magnesium oxide, 19 parts of sodium lauryl sulfate, 12.5 parts of fatty acid polyethylene glycol ester, 18 parts of boric acid alkyl alcohol amide, trichloro 9 parts of fluoromethane, 11 parts of magnesite gel, 7 parts of butylated hydroxyanisole, 7.5 parts of antimony trioxide, 6.5 parts of dibutyl phthalate, 11 parts of lauric acid monoglyceride and 15 parts of butyl acrylate .
[0025] A method for preparing the material of the front ventilating partition of an automobile includes the following steps:
[0026] 1) Combine 50 parts of polypropylene, 11 parts of carbon fiber, 12 parts of polyetherimide, 11 parts of polyar...
Embodiment 3
[0031] A material for the front ventilating partition of an automobile, which is made of the following materials in parts by weight, including 55 parts of polypropylene, 14 parts of carbon fiber, 15 parts of polyetherimide, 12 parts of polyarylate, and polyvinylidene fluoride 25 parts, 10 parts of alkyd resin, 8 parts of dimethyl silicone oil, 15 parts of nano magnesium oxide, 20 parts of sodium lauryl sulfate, 15 parts of fatty acid polyethylene glycol esters, 20 parts of boric acid alkyl alcohol amides, trichloro 11 parts of fluoromethane, 12 parts of magnesite gel, 8 parts of butylated hydroxyanisole, 10 parts of antimony trioxide, 7 parts of dibutyl phthalate, 14 parts of lauric acid monoglyceride and 17 parts of butyl acrylate .
[0032] A method for preparing the material of the front ventilating partition of an automobile includes the following steps:
[0033] 1) Combine 55 parts of polypropylene, 14 parts of carbon fiber, 15 parts of polyetherimide, 12 parts of polyarylate...
PUM
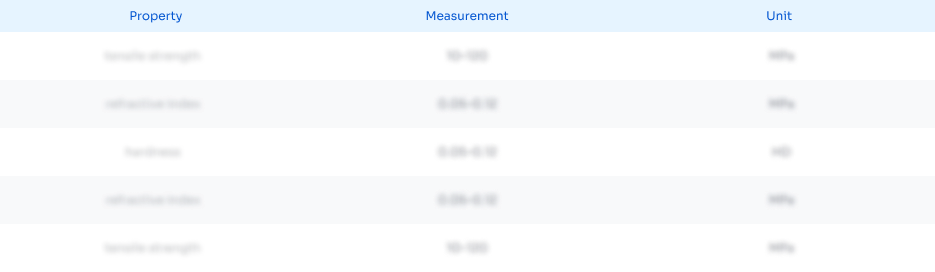
Abstract
Description
Claims
Application Information

- Generate Ideas
- Intellectual Property
- Life Sciences
- Materials
- Tech Scout
- Unparalleled Data Quality
- Higher Quality Content
- 60% Fewer Hallucinations
Browse by: Latest US Patents, China's latest patents, Technical Efficacy Thesaurus, Application Domain, Technology Topic, Popular Technical Reports.
© 2025 PatSnap. All rights reserved.Legal|Privacy policy|Modern Slavery Act Transparency Statement|Sitemap|About US| Contact US: help@patsnap.com