Cast copper rotor of motor
A technology of electric motors and copper casting, which is applied to the rotating parts of the magnetic circuit, the shape/style/structure of the magnetic circuit, etc., can solve the problems of copper strips moving in the slot, copper strips moving, and hidden dangers of long-term operation of the motor, etc., to achieve Improvement of reliability and service life, effect of improving reliability
- Summary
- Abstract
- Description
- Claims
- Application Information
AI Technical Summary
Problems solved by technology
Method used
Image
Examples
Embodiment Construction
[0019] The present invention will be further described below according to the accompanying drawings and in conjunction with the embodiments.
[0020] The cast copper rotor of the motor shown in the accompanying drawings includes a rotor core 1; the rotor core 1 is formed by laminating several rotor punches 2 of the same size and shape; the middle part of the rotor punch 2 is provided with shaft holes 2.2, which are evenly distributed There are several guide bar holes 2.1. In this embodiment, the orifices of the guide bar holes 2.1 around the rotor punching sheet 2 adopt a shrinking structure (the width of the opening is smaller than the inner width of the guide bar hole 2.1), and each rotor punching sheet 2 The guide bar holes 2.1 are stacked to form guide bar grooves in the rotor core 1; the inner wall of the rotor punch 2 shaft hole 2.2 is provided with a keyway 2.3, and in this embodiment, the inner wall of the rotor punch 2 shaft hole 2.2 is provided with a relative Rotor ...
PUM
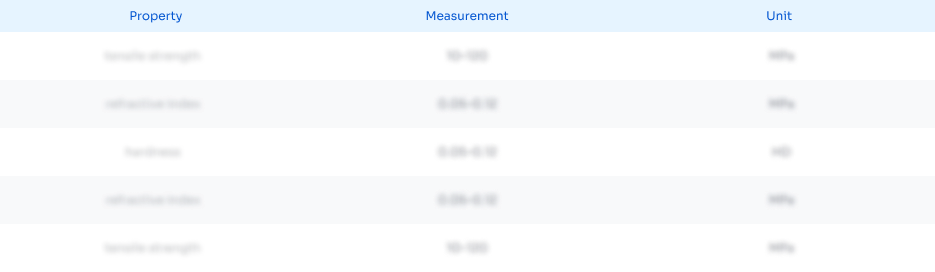
Abstract
Description
Claims
Application Information

- R&D Engineer
- R&D Manager
- IP Professional
- Industry Leading Data Capabilities
- Powerful AI technology
- Patent DNA Extraction
Browse by: Latest US Patents, China's latest patents, Technical Efficacy Thesaurus, Application Domain, Technology Topic, Popular Technical Reports.
© 2024 PatSnap. All rights reserved.Legal|Privacy policy|Modern Slavery Act Transparency Statement|Sitemap|About US| Contact US: help@patsnap.com