Automatic windshield for extrusion head line inlet
A technology of extruder head and wire inlet, which is applied in the field of automatic windshield devices, can solve the problems of cable breakdown, cable bulge, and reduce product qualification rate, etc., and achieves the effects of convenient disassembly, convenient installation and simple internal structure
- Summary
- Abstract
- Description
- Claims
- Application Information
AI Technical Summary
Problems solved by technology
Method used
Image
Examples
Embodiment Construction
[0018] see figure 1 - Figure 7 , the present invention is an automatic wind-shielding device for the wire inlet of an extruder, comprising a square metal box body 10 and a metal cover plate 20 mounted on the square metal box body 10; the square metal box body 10 has a metal Bottom plate 11 and upper, lower, left and right four metal side plates 12,13,14,15 that link to each other with metal base plate 11, every piece of metal side plate 12,13,14,15 along the approximate central position of lengthwise direction passes solid The loaded spring 16 is equipped with metal windshields 17, and the board surfaces of these four metal windshields 17 are all parallel to the board surfaces of the metal bottom plate 11 and are respectively located in different planes; the metal cover plate 20 and the metal bottom plate 11 The central position of each is provided with equal-diameter inlet and outlet holes 1 and 2, the width of each metal windshield 17 is equal to the diameter of the inlet ...
PUM
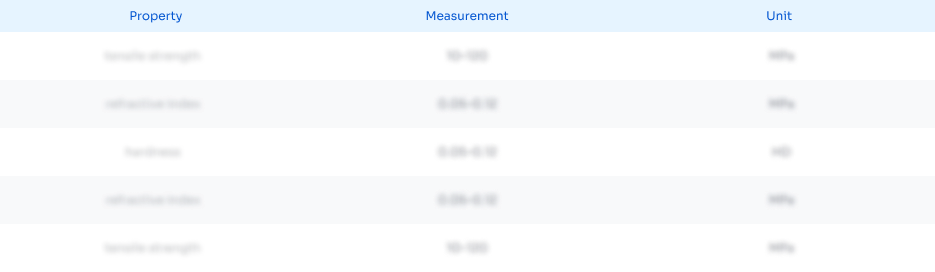
Abstract
Description
Claims
Application Information

- R&D Engineer
- R&D Manager
- IP Professional
- Industry Leading Data Capabilities
- Powerful AI technology
- Patent DNA Extraction
Browse by: Latest US Patents, China's latest patents, Technical Efficacy Thesaurus, Application Domain, Technology Topic, Popular Technical Reports.
© 2024 PatSnap. All rights reserved.Legal|Privacy policy|Modern Slavery Act Transparency Statement|Sitemap|About US| Contact US: help@patsnap.com